Novel formwork drying system
A drying system and mold shell technology, applied in the directions of casting molds, cores, casting mold components, etc., can solve problems such as uneven drying, and achieve the effects of shortening drying time, short drying time, and not easy to dissipate heat.
- Summary
- Abstract
- Description
- Claims
- Application Information
AI Technical Summary
Problems solved by technology
Method used
Image
Examples
Embodiment Construction
[0035] Such as figure 1 , 2 As shown, a new mold shell drying system described in the present invention is suitable for figure 2 The fifth step in the process is drying after shell making. The system components include: drying room body 1, remote control door 2, insulation wall 3, observation window 4, temperature and humidity display panel 5, timer 6, dehumidifier 7, 8, air conditioner 9. Temperature alarm 10, auxiliary ventilation pipeline 11, blower 12; the drying room body 1 is surrounded by insulation walls 3, and its left and right sides and rear insulation walls 3 are all airtight;
[0036] The middle position of the front of the drying room body 1 is provided with a remote control door 2, and an observation window 4 is provided on the insulation wall 3 on both sides of the remote control door 2, and a timer 6 is arranged on the top of the remote control door 2. The right side is provided with a temperature and humidity display panel 5, and the temperature and humidi...
PUM
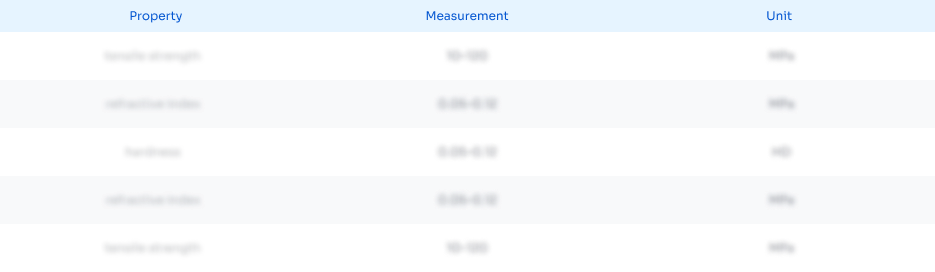
Abstract
Description
Claims
Application Information

- R&D
- Intellectual Property
- Life Sciences
- Materials
- Tech Scout
- Unparalleled Data Quality
- Higher Quality Content
- 60% Fewer Hallucinations
Browse by: Latest US Patents, China's latest patents, Technical Efficacy Thesaurus, Application Domain, Technology Topic, Popular Technical Reports.
© 2025 PatSnap. All rights reserved.Legal|Privacy policy|Modern Slavery Act Transparency Statement|Sitemap|About US| Contact US: help@patsnap.com