Simulated test platform for axial winding deformation of transformer
A transformer winding, axial deformation technology, applied in the direction of electric/magnetic solid deformation measurement, instrument, measurement of electric variables, etc., can solve problems such as difficulty in convenient simulation, trouble, and limit the development and improvement of winding deformation detection technology
- Summary
- Abstract
- Description
- Claims
- Application Information
AI Technical Summary
Problems solved by technology
Method used
Image
Examples
Embodiment Construction
[0017] The present invention will be described in detail below with reference to the drawings and embodiments.
[0018] Such as figure 2 , A simulation test platform for transformer winding deformation, consisting of 110kV winding (1) of a real power transformer, transformer oil tank (2), 110kV high voltage bushing (3), 10kV low voltage bushing (4), epoxy glass It is composed of a fiber rod push rod (5), a soft ferrite deformation block (6) and a dynamic sealing mechanism (7). The height of the winding is 1080mm, and the outer diameter is 1150mm; the fuel tank (2) is a square box made of iron. The minimum gap between the winding (1) and the fuel tank (2) is 240mm; the dynamic sealing mechanism (7) includes a through flange of the fuel tank wall and an O-shaped rubber sealing ring, which can ensure easy control of the push rod (5) extending into or out of the winding ( 1) Placed inside the fuel tank (2), and lead the high-voltage lead of the winding (1) out of the fuel tank (2)...
PUM
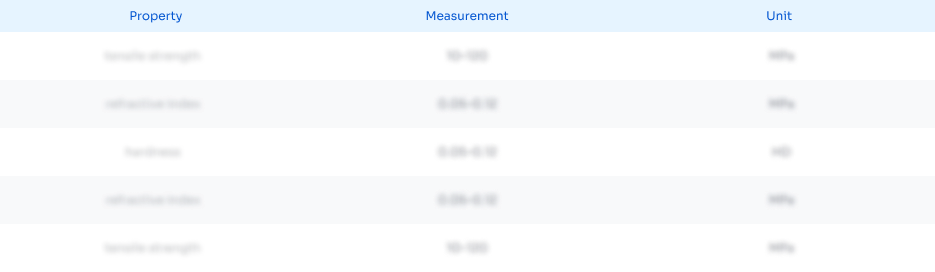
Abstract
Description
Claims
Application Information

- R&D Engineer
- R&D Manager
- IP Professional
- Industry Leading Data Capabilities
- Powerful AI technology
- Patent DNA Extraction
Browse by: Latest US Patents, China's latest patents, Technical Efficacy Thesaurus, Application Domain, Technology Topic, Popular Technical Reports.
© 2024 PatSnap. All rights reserved.Legal|Privacy policy|Modern Slavery Act Transparency Statement|Sitemap|About US| Contact US: help@patsnap.com