Sealing device for rolling mill CVC shifting roller coupling mechanism
A technology of coupling mechanism and sealing device, which is applied in the direction of metal rolling mill stand, engine seal, metal rolling stand, etc., can solve the problems of increased grease consumption and economic cost, damaged skeleton seal, poor lubrication, etc., and saves spare parts Cost and maintenance time, extended service life, improved sealing effect
- Summary
- Abstract
- Description
- Claims
- Application Information
AI Technical Summary
Problems solved by technology
Method used
Image
Examples
Embodiment Construction
[0032] Figure 2 to Figure 5 It is shown that the present invention includes a bearing housing 5, a thrust spherical roller bearing 4 installed inside the bearing housing 5, a coupling inner sleeve 6, a roller side inner sleeve 7 set on the right side of the coupling inner sleeve 6, a transparent cover 8, and a gland 9. The sealing sleeve 10, the left compensation sealing sleeve 11 and the right compensation sealing sleeve 12, and the thrust self-aligning roller shaft, 4 are set on the outer circumference of the coupling inner sleeve 6.
[0033] Figure 5 , Figure 10 and Figure 11 It is shown that the inner sleeve 7 on the roller side is connected by two sleeves with different outer diameters, the sleeve with a smaller outer diameter is inserted into the coupling inner sleeve 6, and the inner circumference of the joint of the two sleeves is fixed with the inner sleeve on the roller side. 7 coaxial rings, 6 axial screw holes are equidistantly provided on the ring, which ar...
PUM
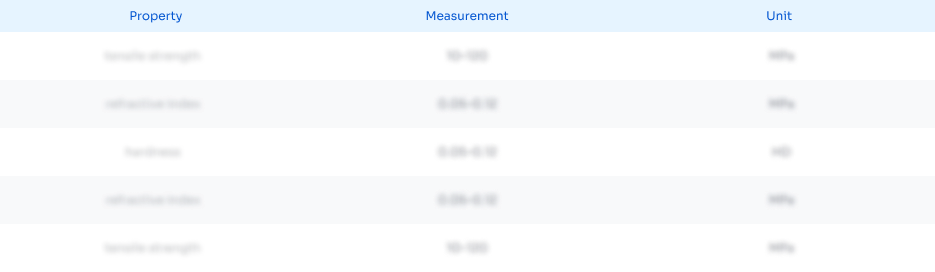
Abstract
Description
Claims
Application Information

- Generate Ideas
- Intellectual Property
- Life Sciences
- Materials
- Tech Scout
- Unparalleled Data Quality
- Higher Quality Content
- 60% Fewer Hallucinations
Browse by: Latest US Patents, China's latest patents, Technical Efficacy Thesaurus, Application Domain, Technology Topic, Popular Technical Reports.
© 2025 PatSnap. All rights reserved.Legal|Privacy policy|Modern Slavery Act Transparency Statement|Sitemap|About US| Contact US: help@patsnap.com