Method for rapidly manufacturing mold through 3D printing materials
A 3D printing and mold technology, which is applied in the direction of manufacturing tools, additive processing, casting molding equipment, etc., can solve the problems that the quality and efficiency cannot be improved, and achieve the effects of saving production time, reducing production costs, and ensuring strength
- Summary
- Abstract
- Description
- Claims
- Application Information
AI Technical Summary
Problems solved by technology
Method used
Image
Examples
Embodiment
[0027] The structure diagram of the present invention is as figure 1 , 2 , 3, and 4, the method for quickly making molds using 3D printing materials of the present invention includes the following steps:
[0028] 1) Design the mold model through CAD;
[0029] 2) Design the CAD mold model as a mold shell model;
[0030] 3) After adding fixtures to the thin shell model of the mold, print the mold cavity with 3D printing equipment;
[0031] 4) Process the upper mold core with CNC;
[0032] 5) Fix the mold cavity and the upper mold core on the standard mold frame;
[0033] 6) Fill sand on the back of the mold cavity and solidify;
[0034] 7) A cover plate is installed on the back of the mold cavity, and the cover plate is fixed on the standard mold frame through the first connecting piece;
[0035] 8) Complete the mold making.
[0036] In this embodiment, in the above step 5), the upper mold core is first fixed on the mold cavity, and then the mold cavity is fixed on the st...
PUM
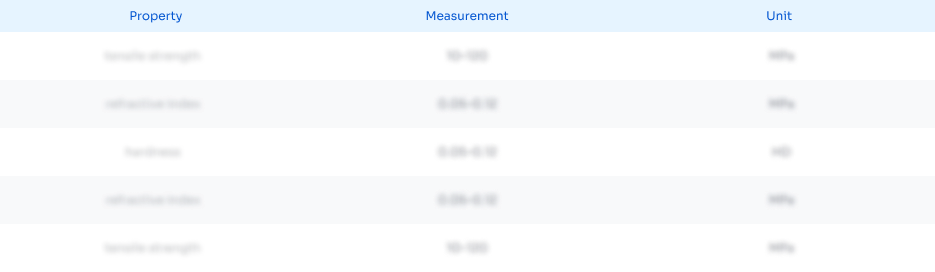
Abstract
Description
Claims
Application Information

- Generate Ideas
- Intellectual Property
- Life Sciences
- Materials
- Tech Scout
- Unparalleled Data Quality
- Higher Quality Content
- 60% Fewer Hallucinations
Browse by: Latest US Patents, China's latest patents, Technical Efficacy Thesaurus, Application Domain, Technology Topic, Popular Technical Reports.
© 2025 PatSnap. All rights reserved.Legal|Privacy policy|Modern Slavery Act Transparency Statement|Sitemap|About US| Contact US: help@patsnap.com