Printing and dyeing wastewater treatment process
A treatment process, printing and dyeing wastewater technology, applied in textile industry wastewater treatment, multi-stage water treatment, water/sewage treatment, etc., can solve the problems of poor effluent quality and high treatment costs, achieve good flocculation, good oxidation, and reduce The effect of chroma
- Summary
- Abstract
- Description
- Claims
- Application Information
AI Technical Summary
Problems solved by technology
Method used
Examples
Embodiment 1
[0020] Step 1: In the initial state, the printing and dyeing wastewater with a CODGr of 1200 mg / L, a BOD5 of 250 mg / L, and a pH of 10 is filtered through a grid and then pumped into a regulating tank and adjusted to a pH of 8.0;
[0021] Step 2: Pump the wastewater in step 1 into the closed faeciform tank and put into activated sludge, and make the waste water stay in the facultative tank for 6 hours;
[0022] Step 3: pump the wastewater in step 2 into a high-efficiency anaerobic bioreactor, and remove impurities in the wastewater through anaerobic treatment;
[0023] Step 4: discharge the effluent from the high-efficiency anaerobic bioreactor.
Embodiment 2
[0025] Step 1: In the initial state, the printing and dyeing wastewater with a CODGr of 1000 mg / L, a BOD5 of 320 mg / L, and a pH of 11 is filtered through a grid and then pumped into a regulating tank and adjusted to a pH of 7.8;
[0026] Step 2: Pump the waste water in step 1 into the primary reaction tank, and add activated sludge. After standing for 0.5 hours, add Mg2SO4 with a waste water volume of 3g / m3 and feed 120V direct current at the same time, so that the waste water stays for 4 hours;
[0027] Step 3: pump the waste water in step 2 into the closed aerobic tank, and make the waste water stay in the aerobic tank for 4 hours;
[0028] Step 4: pump the wastewater in step 3 into a high-efficiency anaerobic bioreactor, and remove impurities in the wastewater through anaerobic treatment;
[0029] Step 5: Discharging the effluent from the high-efficiency anaerobic bioreactor.
Embodiment 3
[0031] Step 1: In the initial state, the printing and dyeing wastewater with a CODGr of 1400 mg / L, a BOD5 of 180 mg / L, and a pH of 9 is filtered through a grid and then pumped into a regulating tank and adjusted to a pH of 8.2;
[0032] Step 2: Pump the waste water in step 1 into the primary reaction tank, and add activated sludge, after standing for 0.5h, add FeSO4 with 1g / m3 of waste water and feed 140V direct current at the same time, make the waste water stay for 2.5h;
[0033] Step 3: pump the waste water in step 2 into the closed aerobic tank, and make the waste water stay in the aerobic tank for 5 hours;
[0034] Step 4: pump the wastewater in step 3 into a high-efficiency anaerobic bioreactor, and remove impurities in the wastewater through anaerobic treatment;
[0035] Step 5: Discharging the effluent from the high-efficiency anaerobic bioreactor.
PUM
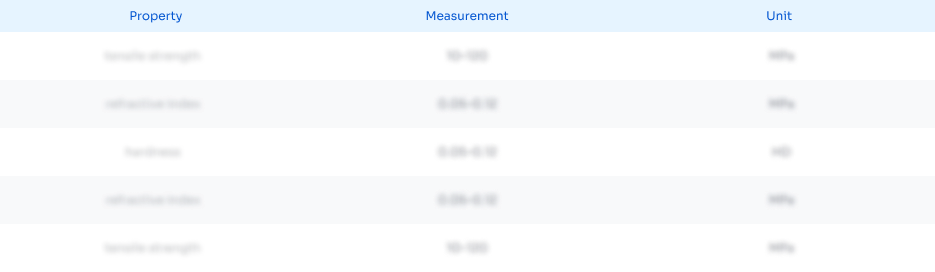
Abstract
Description
Claims
Application Information

- R&D Engineer
- R&D Manager
- IP Professional
- Industry Leading Data Capabilities
- Powerful AI technology
- Patent DNA Extraction
Browse by: Latest US Patents, China's latest patents, Technical Efficacy Thesaurus, Application Domain, Technology Topic, Popular Technical Reports.
© 2024 PatSnap. All rights reserved.Legal|Privacy policy|Modern Slavery Act Transparency Statement|Sitemap|About US| Contact US: help@patsnap.com