Hydrodesulfurization and dearomatization catalyst and system, preparation method thereof, and method for hydrodesulfurization and dearomatization of diesel oil
A hydrodesulfurization and dearomatization technology, applied in chemical instruments and methods, physical/chemical process catalysts, hydrocarbon oil treatment, etc., can solve the problems of catalysts that cannot take into account the effects of desulfurization and dearomatization, and the low proportion of multi-layer stacking activity , to achieve the effect of low aromatics content, low sulfur and aromatics content, and increase the degree of sulfidation
- Summary
- Abstract
- Description
- Claims
- Application Information
AI Technical Summary
Problems solved by technology
Method used
Examples
preparation example Construction
[0040] According to the preparation method of the catalyst of the present invention, preferably, the method further includes increasing the temperature at a rate of 1-20°C / h from the temperature corresponding to the highest exothermic peak of the alcohol compound by 20-150 °C is preferably 1-10 °C, more preferably 5-10 °C and is kept constant for 1-15 h, preferably 1-10 hours.
[0041] By adopting a multi-stage sulfuration method, the degree of sulfuration of the metal in the catalyst is increased, so the catalyst has a high number of active centers.
[0042] In order to improve the activity of the catalyst, a special sulfidation step is taken in the present invention. This method can convert more active metals in the oxidized catalyst into a sulfurized state, increase the number of active components, and increase the ratio of the three-layer stacked active phase, so that the catalyst exhibits higher hydrodesulfurization and aromatic hydrocarbon saturation activities.
[0043...
Embodiment 1
[0083] The alcohol compound contained in catalyst A1 is ethylene glycol, the content of cobalt oxide is 3%, and the content of molybdenum oxide is 17%. 2 o 3 Content is 1.5%, P 2 o 5 The content is 6%, and the molar ratio of ethylene glycol to cobalt is 1:1.
[0084] Catalyst B1 contains nickel oxide 3%, molybdenum oxide content is 17%, B 2 o 3 Content is 1.5%, P 2 o 5 The content is 6%, and the molar ratio of ethylene glycol to nickel is 1:1.
[0085] The above-mentioned catalyst is determined by temperature-programmed oxidation experiments, and it can decompose and release CO between 230-300°C and 300-400°C. 2 , and the release temperatures were 260°C and 350°C, respectively.
[0086] Catalyst A1 is packed in the upper bed, catalyst B1 is packed in the lower bed, and the volume ratio of catalyst A1 to catalyst B1 is 1:1.
[0087] The activity evaluation of the catalyst system was carried out on a 20mL high-pressure hydrodesulfurization evaluation device. Before the...
Embodiment 2
[0101] The alcohol contained in the catalyst A2 is glycerol, the content of cobalt oxide is 6%, the content of molybdenum oxide is 25%, the content of MgO is 1.9%, and the molar ratio of glycerol to cobalt is 1.5:1.
[0102] Catalyst B2 contains 6% nickel oxide, 25% molybdenum oxide, 1.9% MgO, and a molar ratio of glycerol to nickel of 1.5:1.
[0103] Catalyst A2 is packed in the upper bed, catalyst B2 is packed in the lower bed, and the volume ratio of catalyst A2 to catalyst B2 is 2:1.
[0104] According to the temperature-programmed oxidation test, the catalysts decompose and release CO at 265°C and 345°C respectively. 2 . The vulcanization conditions and activity test conditions are the same as in Example 1, and the vulcanization program is changed to: heat up to 265°C at a heating rate of 8°C / h and then keep the temperature for 3h, then raise the temperature to 345°C at a heating rate of 5°C / h and keep the temperature constant After 2.5 hours, the temperature was raised...
PUM
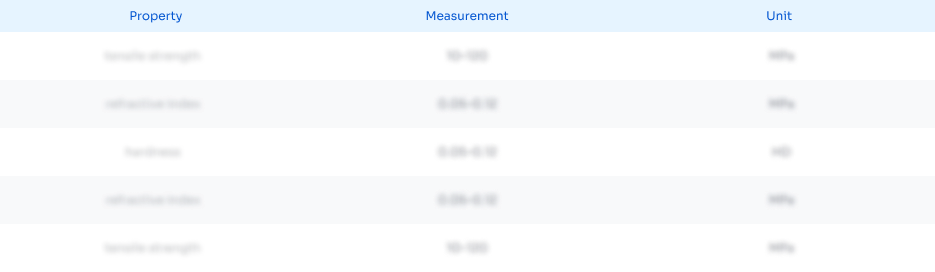
Abstract
Description
Claims
Application Information

- R&D
- Intellectual Property
- Life Sciences
- Materials
- Tech Scout
- Unparalleled Data Quality
- Higher Quality Content
- 60% Fewer Hallucinations
Browse by: Latest US Patents, China's latest patents, Technical Efficacy Thesaurus, Application Domain, Technology Topic, Popular Technical Reports.
© 2025 PatSnap. All rights reserved.Legal|Privacy policy|Modern Slavery Act Transparency Statement|Sitemap|About US| Contact US: help@patsnap.com