Method and system for varnish dipping of motor with winding stator
A winding and stator technology, which is applied in the field of stator varnish dipping method and system, can solve the problems of less paint hanging on the winding stator, the inability to solve the dipping paint quality, and reduce production efficiency, so as to avoid insufficient varnish hanging on winding windings Avoid insufficient winding paint and ensure the quality of dipping paint
- Summary
- Abstract
- Description
- Claims
- Application Information
AI Technical Summary
Problems solved by technology
Method used
Image
Examples
Embodiment Construction
[0011] The following is attached figure 1 The present invention is further explained.
[0012] First, the method of dipping the winding stator is explained:
[0013] A method for dipping a motor with a winding stator includes pre-baking, cooling, vacuum dipping, paint dripping, and baking processes. At least the winding stator in the front part of the baking process runs in a horizontal rotating state until the initial setting state of the dipping paint is reached.
[0014] The winding stator undergoes a pre-baking operation, which can effectively evaporate the water on the winding stator. The pre-baked winding stator can be cooled to ensure the dipping quality of the winding stator. Through the vacuum dipping of the stator winding, After the vacuum dipping operation, the amount of paint on the winding stator is too much, and the paint on the winding stator will naturally drip down. When the paint dripping on the winding is almost the same, the winding stator is baked, and when the ...
PUM
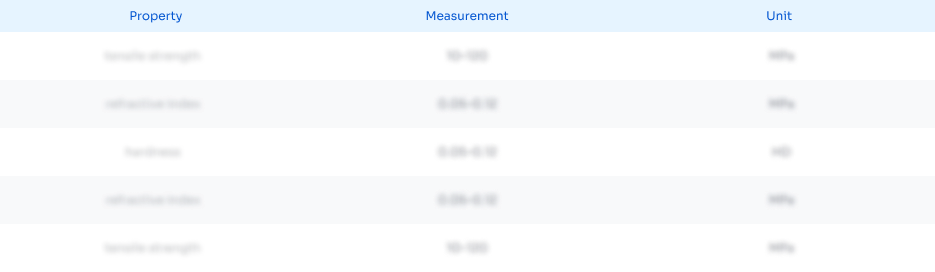
Abstract
Description
Claims
Application Information

- R&D
- Intellectual Property
- Life Sciences
- Materials
- Tech Scout
- Unparalleled Data Quality
- Higher Quality Content
- 60% Fewer Hallucinations
Browse by: Latest US Patents, China's latest patents, Technical Efficacy Thesaurus, Application Domain, Technology Topic, Popular Technical Reports.
© 2025 PatSnap. All rights reserved.Legal|Privacy policy|Modern Slavery Act Transparency Statement|Sitemap|About US| Contact US: help@patsnap.com