A kind of production method of wear-resistant aluminum alloy
A production method and aluminum alloy technology, which is applied in the field of alloy manufacturing, can solve problems such as large differences in mechanical properties, overheating of parts, and large differences in spatial distribution, so as to achieve excellent abnormal temperature mechanical properties and improve the mechanical properties of alloys.
- Summary
- Abstract
- Description
- Claims
- Application Information
AI Technical Summary
Problems solved by technology
Method used
Image
Examples
Embodiment 1
[0017] A wear-resistant aluminum alloy, composed of the following components according to mass percentage: 3.89% iron, 10.65% zinc, 9.99% copper, 1.42% iridium, 0.57% tungsten, 0.31% erbium, 1.12% ruthenium, 0.55% cobalt, and the balance for aluminum.
[0018] A method for preparing a wear-resistant aluminum alloy, comprising the following steps:
[0019] 1) Put iron, zinc, copper, tungsten, aluminum, etc. into the crucible of the vacuum melting furnace, and evacuate to 8×10 -2 Above Pa, start to heat up. After the temperature rises to 865°C, stop vacuuming and fill the vacuum melting furnace with inert gas to 4×10 4 Pa; then continue to heat up to 1280 ° C to form an alloy liquid, fill the alloy liquid with an inert gas and stir for 35 minutes, cool the alloy liquid to obtain an intermediate alloy;
[0020] 2) Add the master alloy, erbium, ruthenium, and cobalt into the crucible of the vacuum melting furnace, and evacuate to 8×10 -2 Above Pa, start to heat up. After the te...
Embodiment 2
[0024] A zinc alloy for die-casting, consisting of the following components according to mass percentage: 3.99% iron, 10.65% zinc, 10% copper, 1.35% iridium, 0.56% tungsten, 0.315% erbium, 1.12% ruthenium, 0.51% cobalt, and The amount is aluminum.
[0025] The preparation method is the same as in Example 1.
Embodiment 3
[0027] A wear-resistant aluminum alloy, consisting of the following components according to mass percentage: 3.56% iron, 10.45% zinc, 9.85% copper, 1.38% iridium, 0.48% tungsten, 0.31% erbium, 1.09% ruthenium, 0.55% cobalt, and the balance for aluminum.
[0028] The preparation method is the same as in Example 1.
PUM
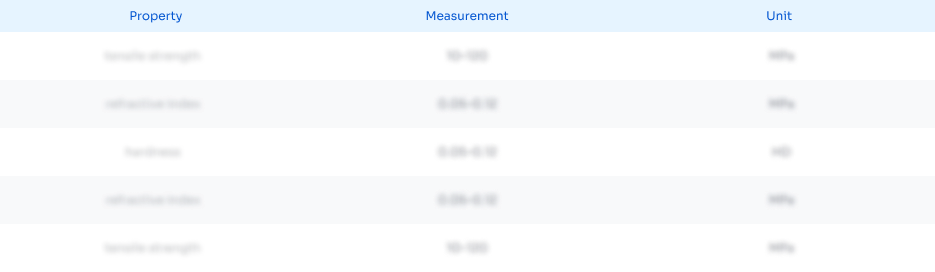
Abstract
Description
Claims
Application Information

- Generate Ideas
- Intellectual Property
- Life Sciences
- Materials
- Tech Scout
- Unparalleled Data Quality
- Higher Quality Content
- 60% Fewer Hallucinations
Browse by: Latest US Patents, China's latest patents, Technical Efficacy Thesaurus, Application Domain, Technology Topic, Popular Technical Reports.
© 2025 PatSnap. All rights reserved.Legal|Privacy policy|Modern Slavery Act Transparency Statement|Sitemap|About US| Contact US: help@patsnap.com