Non-structural mass trimming method for airplane in steady overload state
A non-structural and aircraft technology, applied in the field of non-structural mass trimming of aircraft under constant overload state, can solve problems such as reducing the calculation accuracy of design analysis results, incorrect stress concentration deformation of related elements of constraint nodes, and inappropriate force transmission routes.
- Summary
- Abstract
- Description
- Claims
- Application Information
AI Technical Summary
Problems solved by technology
Method used
Image
Examples
Embodiment Construction
[0063] This embodiment describes the technical solution of the present invention in detail through the non-structural mass trimming process of a certain type of unmanned aerial vehicle in a steady overload state.
[0064] This embodiment is specifically aimed at the UAV CAD data, overload coefficient and aerodynamic load given by a user, and completes the force analysis and design process of the UAV in a free flight state through the non-structural mass balance method. The specific process includes the following steps:
[0065] Step 1, division of finite element unstructured mesh. According to the UAV CAD data given by the user, Hypermesh software is used to divide the UAV CAD geometric model into a finite element unstructured mesh. The geometry of the drone is figure 1 As shown, the internal skeleton is as figure 2 shown. The UAV is divided into three sections: fuselage, inner wing, and outer wing. The length of the fuselage is 3.893m. The main load-bearing components o...
PUM
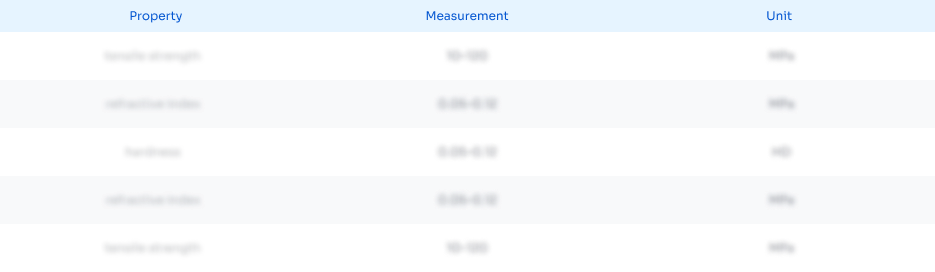
Abstract
Description
Claims
Application Information

- R&D
- Intellectual Property
- Life Sciences
- Materials
- Tech Scout
- Unparalleled Data Quality
- Higher Quality Content
- 60% Fewer Hallucinations
Browse by: Latest US Patents, China's latest patents, Technical Efficacy Thesaurus, Application Domain, Technology Topic, Popular Technical Reports.
© 2025 PatSnap. All rights reserved.Legal|Privacy policy|Modern Slavery Act Transparency Statement|Sitemap|About US| Contact US: help@patsnap.com