Continuous reforming process for hydrocarbons
A process and technology of hydrocarbons, applied in the field of continuous reforming process of hydrocarbons, can solve the problems of continuous reforming process, etc., and achieve the effect of improving reforming conversion rate and product yield, improving efficiency and reducing carbon deposition
- Summary
- Abstract
- Description
- Claims
- Application Information
AI Technical Summary
Problems solved by technology
Method used
Image
Examples
Embodiment
[0067] This embodiment combines the attached image 3 A specific implementation manner provided by the present invention will be described. Since what is carried out is a long-term industrial experiment, the various process operating conditions described therein allow about ±10% fluctuation.
[0068] Such as image 3 As shown, the reaction feed passes through the first reaction heating furnace 2, the first reforming reactor 3, the second reaction heating furnace 4, and the second reforming furnace successively after exchanging heat with the reaction product in the reaction feed / product heat exchanger 1. Whole reactor 5, the 3rd reaction heating furnace 6, the 3rd reforming reactor 7, the 4th reaction heating furnace 8 and the 4th reforming reactor 9, after the reaction product leaves the 4th reforming reactor 9, in reaction feeding / Product heat exchanger 1 exchanges heat with the reaction feed, and then goes to the subsequent separation device for separation. Reactants pro...
PUM
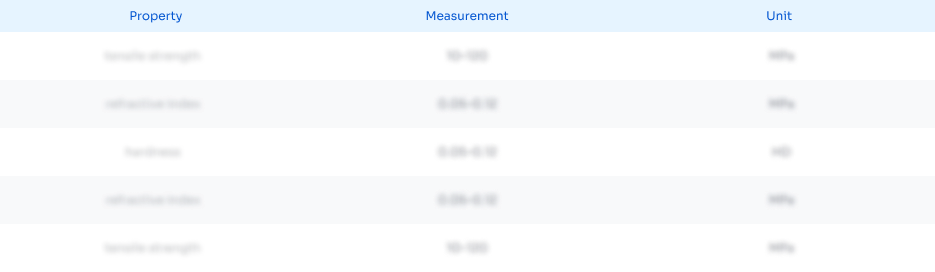
Abstract
Description
Claims
Application Information

- R&D Engineer
- R&D Manager
- IP Professional
- Industry Leading Data Capabilities
- Powerful AI technology
- Patent DNA Extraction
Browse by: Latest US Patents, China's latest patents, Technical Efficacy Thesaurus, Application Domain, Technology Topic, Popular Technical Reports.
© 2024 PatSnap. All rights reserved.Legal|Privacy policy|Modern Slavery Act Transparency Statement|Sitemap|About US| Contact US: help@patsnap.com