Method for accurately forecasting five-axis processing milling force of spiral cutter
A prediction method, the technology of helical milling cutter, applied in special data processing applications, instruments, electrical digital data processing, etc., can solve problems such as difficulty, unfavorable rapid prediction of milling force, and huge calculation time.
- Summary
- Abstract
- Description
- Claims
- Application Information
AI Technical Summary
Problems solved by technology
Method used
Image
Examples
Embodiment Construction
[0047] The present invention is described in further detail below in conjunction with accompanying drawing:
[0048] The method for accurately predicting the milling force of the five-axis machining of the helical milling cutter according to the present invention comprises the following steps:
[0049] 1) Obtain the tool rotation coordinate system X according to the tool eccentric state r Y r Z r The coordinates of the tool edge line in ;
[0050] 2) The instantaneous trajectory equation of the edge line including the tool eccentricity parameter is obtained from the instantaneous tool tip position and the angular position of the pendulum axis;
[0051] 3) Any given cutting point has been established And the parametric equation of a straight line l perpendicular to the tool axis;
[0052] 4) Obtain the position of the intersection point T of the straight line l and the adjacent front mi knife edge trajectories through the linear iterative method according to the edge line...
PUM
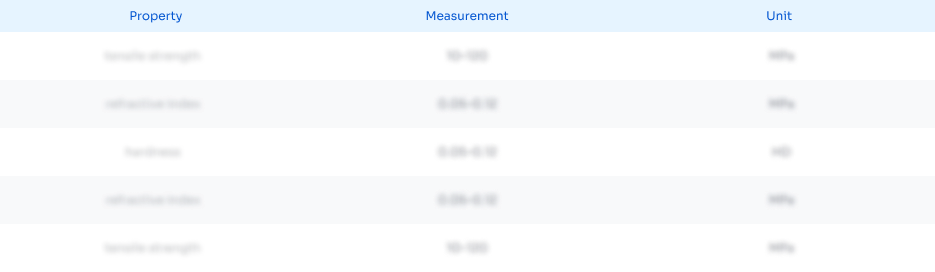
Abstract
Description
Claims
Application Information

- R&D
- Intellectual Property
- Life Sciences
- Materials
- Tech Scout
- Unparalleled Data Quality
- Higher Quality Content
- 60% Fewer Hallucinations
Browse by: Latest US Patents, China's latest patents, Technical Efficacy Thesaurus, Application Domain, Technology Topic, Popular Technical Reports.
© 2025 PatSnap. All rights reserved.Legal|Privacy policy|Modern Slavery Act Transparency Statement|Sitemap|About US| Contact US: help@patsnap.com