Secondary air offset whirl pulverized coal burner for W flame boiler
A technology of pulverized coal burner and secondary air, which is applied in the direction of burner, burner, and combustion type of powdered fuel, and can solve problems such as slagging, high-temperature corrosion, high content of fly ash combustibles, and high NOx emissions , to achieve the effects of improving flame stability, reducing the content of fly ash combustibles, and reducing the amount of NOx generated
- Summary
- Abstract
- Description
- Claims
- Application Information
AI Technical Summary
Problems solved by technology
Method used
Image
Examples
specific Embodiment approach 1
[0021] Specific implementation mode one: combine figure 1 with figure 2 Describe this embodiment, the primary air 14 of the swirling flow pulverized coal burner 4 of this embodiment and the division cylinder of the inner secondary air 15 are equipped with an annular inner secondary air block along the circumferential direction in the inner secondary air. 8. The circular inner secondary air block 8 has an angle of 180° along the circumferential direction, and a circular ring along the circumferential direction is installed inside the outer secondary air on the division cylinder of the inner secondary air 15 and the outer secondary air 16. The outer secondary wind block 9, the angle of the annular outer secondary wind block 9 along the circumferential direction is 180°, the boundary line of the annular inner secondary wind block 8 and the annular outer secondary wind block 9 along the diameter direction Parallel to the front and rear walls of the boiler, the annular inner seco...
specific Embodiment approach 2
[0022]Specific implementation mode two: combination figure 1 and figure 2 Describe this embodiment, the inner circular wall surface of the inner secondary wind block 8 of this embodiment is close to the outer wall of the primary air duct, and the inner circular wall surface of the outer secondary air block 9 is close to the outer wall of the inner secondary air duct. Other components and connections are the same as those in the first embodiment.
specific Embodiment approach 3
[0023] Specific implementation mode three: combination figure 1 and figure 2 This embodiment is described. In this embodiment, in the axial direction of the primary air pipe of the burner 4 , the front ends of the inner secondary air block 8 and the outer secondary air block 9 are flush with the end of the inner secondary air nozzle 6 . Other components and connections are the same as those in the second embodiment.
PUM
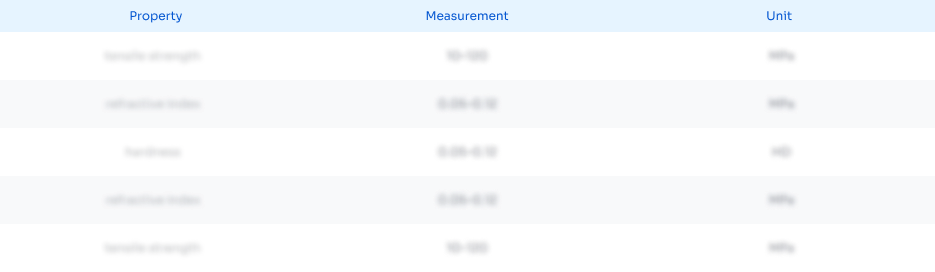
Abstract
Description
Claims
Application Information

- Generate Ideas
- Intellectual Property
- Life Sciences
- Materials
- Tech Scout
- Unparalleled Data Quality
- Higher Quality Content
- 60% Fewer Hallucinations
Browse by: Latest US Patents, China's latest patents, Technical Efficacy Thesaurus, Application Domain, Technology Topic, Popular Technical Reports.
© 2025 PatSnap. All rights reserved.Legal|Privacy policy|Modern Slavery Act Transparency Statement|Sitemap|About US| Contact US: help@patsnap.com