Welding and overturning device for crane beam
A technology of overturning device and crane girder, which is applied in the direction of hoisting device, auxiliary device, hoisting device, etc., can solve the problems of collision between crane girder and overturning device, inconvenient fixing of crane girder, sliding friction of crane girder, etc., and achieve protection of overturning device, Simple structure, avoiding the effect of sliding friction
- Summary
- Abstract
- Description
- Claims
- Application Information
AI Technical Summary
Problems solved by technology
Method used
Image
Examples
Embodiment 1
[0019] Such as Figure 1-3 As shown, a crane girder welding overturning device includes a base 1, and the upper surface of the base 1 is symmetrically provided with a support A2 and a support B3, and the bearings in the support A2 and the support B3 are A rotating shaft A4 and a rotating shaft B5 are respectively provided, and the ends of the rotating shaft A4 and the rotating shaft B5 are respectively connected with an angle sensor A6 and an angle sensor B7, and the angle sensor A6 and the angle sensor B7 are connected with a controller 8 , the middle part of the rotating shaft A4 and the rotating shaft B5 is respectively connected with an overturning frame A9 and an overturning frame B10, the described overturning frame A9 is arranged as an L-shaped structure, and the bending part of the overturning frame A9 is connected with an overturning push rod A11, and the described The end of overturning push rod A11 is hingedly connected with hydraulic cylinder A12, and the upper sur...
Embodiment 2
[0022] Such as Figure 1-3 As shown, a crane girder welding overturning device includes a base 1, and the upper surface of the base 1 is symmetrically provided with a support A2 and a support B3, and the bearings in the support A2 and the support B3 are A rotating shaft A4 and a rotating shaft B5 are respectively provided, and the ends of the rotating shaft A4 and the rotating shaft B5 are respectively connected with an angle sensor A6 and an angle sensor B7, and the angle sensor A6 and the angle sensor B7 are connected with a controller 8 , the middle part of the rotating shaft A4 and the rotating shaft B5 is respectively connected with an overturning frame A9 and an overturning frame B10, the described overturning frame A9 is arranged as an L-shaped structure, and the bending part of the overturning frame A9 is connected with an overturning push rod A11, and the described The end of overturning push rod A11 is hingedly connected with hydraulic cylinder A12, and the upper sur...
PUM
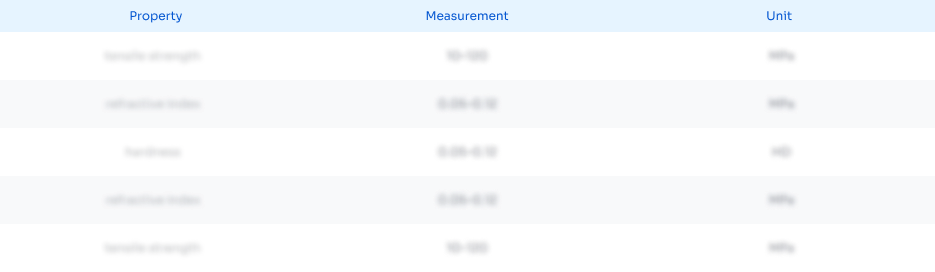
Abstract
Description
Claims
Application Information

- R&D Engineer
- R&D Manager
- IP Professional
- Industry Leading Data Capabilities
- Powerful AI technology
- Patent DNA Extraction
Browse by: Latest US Patents, China's latest patents, Technical Efficacy Thesaurus, Application Domain, Technology Topic, Popular Technical Reports.
© 2024 PatSnap. All rights reserved.Legal|Privacy policy|Modern Slavery Act Transparency Statement|Sitemap|About US| Contact US: help@patsnap.com