Plasticizing and injection molding device
A technology of injection molding seat and plasticizing material, applied in the field of plasticizing injection molding device, can solve the problems of increased production cost, unfavorable product promotion and general use, etc., and achieves the effect of increasing power transmission and low cost
- Summary
- Abstract
- Description
- Claims
- Application Information
AI Technical Summary
Problems solved by technology
Method used
Image
Examples
Embodiment Construction
[0011] Such as figure 1 , 2 As shown, the plasticizing injection molding device includes a plasticizing barrel 1, a plasticizing screw, a front injection molding seat 2, a rear injection molding seat 3, and power components. The rear injection molding seat 3 is slidingly installed on the front injection molding seat 2 through a linear guide rail and a slider; the power part is installed on the rear injection molding seat 3, and it is used to drive the rear injection molding seat 3 to move closer to the front injection molding seat 2 or to move away from the front injection molding seat 2. Action of injection seat 2. The plasticizing barrel 1 is installed on the front injection molding seat 2, one end of the plasticizing screw is installed on the rear injection molding seat 3 and is driven by the power part, the other parts of the plasticizing screw extend into the plasticizing barrel 1, and it Driven to do rotation and translation.
[0012] The power components include plas...
PUM
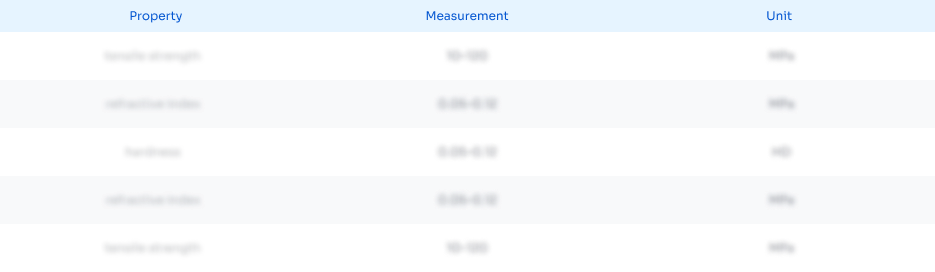
Abstract
Description
Claims
Application Information

- R&D Engineer
- R&D Manager
- IP Professional
- Industry Leading Data Capabilities
- Powerful AI technology
- Patent DNA Extraction
Browse by: Latest US Patents, China's latest patents, Technical Efficacy Thesaurus, Application Domain, Technology Topic, Popular Technical Reports.
© 2024 PatSnap. All rights reserved.Legal|Privacy policy|Modern Slavery Act Transparency Statement|Sitemap|About US| Contact US: help@patsnap.com