Core filling method for solder wire soldering flux
A technology of flux and solder wire, applied in welding equipment, welding medium, welding/cutting medium/material, etc., can solve the problems of high cost and low efficiency of tin wire, improve production efficiency, reduce production cost, and make production simple Effect
- Summary
- Abstract
- Description
- Claims
- Application Information
AI Technical Summary
Problems solved by technology
Method used
Image
Examples
Embodiment
[0051] A solder wire sample with an alloy composition of Sn-Cu0.7 and a flux content of 1.9%±0.2% was prepared.
[0052] Step 1: If Figure 7 As shown, select a hollow tin tube 1 of Sn-Cu0.7 alloy and put it into the hollow tin tube placement frame 2; the length of the hollow tin tube 1 is about 1.2 meters, and the outer diameter is Inner diameter is take one The small round rod of the hollow tin tube 1 and the small hole on the top of the hollow tin tube rack 2 are used to play the role of positioning pins. At this time, pay attention to the gap between the tin tube through hole 11 at the bottom of the hollow tin tube 1 and the taper tip 22. ~2cm distance. Check whether the tin tube through-hole 11 of the hollow tin tube 1 can be accurately stuck on the taper tip 22 when the small round rod is pulled out, and if not, it will be adjusted.
[0053] Step 2: Heat the rosin flux container to be filled to 135-145 degrees;
[0054] Step 3: If Figure 8 As shown, the tin tub...
PUM
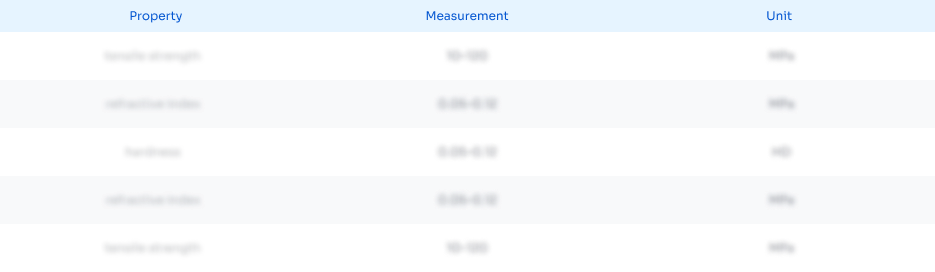
Abstract
Description
Claims
Application Information

- R&D
- Intellectual Property
- Life Sciences
- Materials
- Tech Scout
- Unparalleled Data Quality
- Higher Quality Content
- 60% Fewer Hallucinations
Browse by: Latest US Patents, China's latest patents, Technical Efficacy Thesaurus, Application Domain, Technology Topic, Popular Technical Reports.
© 2025 PatSnap. All rights reserved.Legal|Privacy policy|Modern Slavery Act Transparency Statement|Sitemap|About US| Contact US: help@patsnap.com