Jacket heat exchanger straight pipe inner pipe deep hole welding assembly device and jacket heat exchanger
A technology of heat exchangers and couplers, which is applied in the direction of indirect heat exchangers, heat exchanger types, fixed tubular conduit components, etc., and can solve problems such as difficulty in quality assurance, impossibility of grinding and inspection, and high labor intensity
- Summary
- Abstract
- Description
- Claims
- Application Information
AI Technical Summary
Problems solved by technology
Method used
Image
Examples
Embodiment 1
[0024] A specific embodiment of a jacketed heat exchanger straight tube inner tube deep hole welded assembly of the present application, such as figure 1 As shown, it is used for the pairing between the inner tubes of the straight tubes of the jacketed heat exchanger. The pairing device is arranged symmetrically with the center line of the tube axis. The pairing device includes a conduit 3, a tapered shaft 2 connected to the conduit 3, and The sleeve 1 matched with the taper of the taper shaft 2, the pairing device extends into the inner tube of the straight tube of the jacketed heat exchanger, under the action of external force B, the taper shaft 2 pushes the sleeve 1 to the joint of the two adjacent inner tubes Seam and expand the sleeve 1 at the same time, so that the outer surface of the sleeve 1 is close to the inner wall of the two adjacent inner tubes with straighter two adjacent inner tubes. The external force acts on the conduit 3, and the force is transmitted to the...
Embodiment 2
[0031] A specific embodiment of a jacketed heat exchanger of the present application includes a jacketed heat exchange tube composed of an inner tube and an outer tube, wherein the straight tubes and inner tubes of the jacketed heat exchanger are passed through the above-mentioned embodiment 1 The straight tube inner tube of a jacketed heat exchanger is connected by deep hole welding group to device group butt welding. The jacketed heat exchanger after butt-welding by using the pairing device has the characteristics of good welding quality, high assembly efficiency, long service life and the like.
PUM
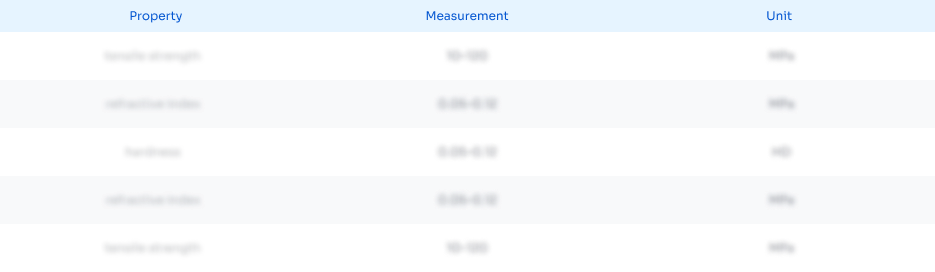
Abstract
Description
Claims
Application Information

- R&D Engineer
- R&D Manager
- IP Professional
- Industry Leading Data Capabilities
- Powerful AI technology
- Patent DNA Extraction
Browse by: Latest US Patents, China's latest patents, Technical Efficacy Thesaurus, Application Domain, Technology Topic, Popular Technical Reports.
© 2024 PatSnap. All rights reserved.Legal|Privacy policy|Modern Slavery Act Transparency Statement|Sitemap|About US| Contact US: help@patsnap.com