Unified-winding bearingless motor and drive control system thereof
A bearingless motor, drive control technology, applied in control systems, vector control systems, motor generator control and other directions, can solve problems such as increasing the hardware complexity of the control system, reducing the number of motor winding turns, and bridge arm straight-through, etc. The effect of making, avoiding straight-through, and simple winding structure
- Summary
- Abstract
- Description
- Claims
- Application Information
AI Technical Summary
Problems solved by technology
Method used
Image
Examples
Embodiment Construction
[0018] In order to make the object, technical solution and advantages of the present invention clearer, the present invention will be further described in detail below in conjunction with the accompanying drawings and embodiments. It should be understood that the specific embodiments described here are only used to explain the present invention, not to limit the present invention. In addition, the technical features involved in the various embodiments of the present invention described below can be combined with each other as long as they do not constitute a conflict with each other.
[0019] In this embodiment, firstly, a bearingless motor with unified winding is provided. The bearingless motor body with unified winding includes a stator 1, a rotor 2, and two displacement sensors 3 with a difference of 90 degrees for measuring the axial position of the rotor offset. Displacement sensor 3 according to as figure 1 The position shown can be used to obtain the displacement of th...
PUM
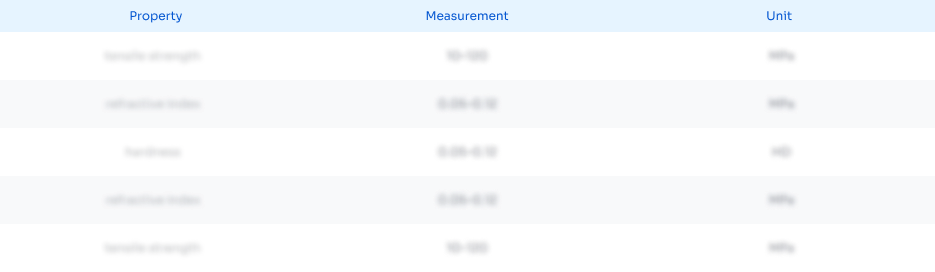
Abstract
Description
Claims
Application Information

- Generate Ideas
- Intellectual Property
- Life Sciences
- Materials
- Tech Scout
- Unparalleled Data Quality
- Higher Quality Content
- 60% Fewer Hallucinations
Browse by: Latest US Patents, China's latest patents, Technical Efficacy Thesaurus, Application Domain, Technology Topic, Popular Technical Reports.
© 2025 PatSnap. All rights reserved.Legal|Privacy policy|Modern Slavery Act Transparency Statement|Sitemap|About US| Contact US: help@patsnap.com