Wire harness adhesive tape winding machine
A technology of winding machine and winding mechanism, applied in the direction of manufacturing wire harnesses, etc., can solve the problems of uneven coverage, abrasion of wire harness products, easy wrinkling of tapes, etc., to achieve good economic benefits, improve production efficiency, and reduce labor intensity.
- Summary
- Abstract
- Description
- Claims
- Application Information
AI Technical Summary
Problems solved by technology
Method used
Image
Examples
Embodiment Construction
[0030] Such as figure 1 As shown, a wire harness tape winding machine is composed of a body 10, a tape winding mechanism, a tape winding drive mechanism, a wire harness traction mechanism and a wire harness 50, wherein a front cover 12 and a rear cover 11 are opened on the top of the body 10 housing, and the tape winding institutions (see figure 2 ) is made up of a tape stand base 20, a tape shaft 23 connected to the tape stand base 20, a short support 24, a long support 25, and a pair of rollers 26 arranged between the short support 24 and the long support 25; the tape winding drive mechanism is composed of The first motor 31, the driving pulley 32 driven by the first motor 31 to rotate, the belt 33 and the driven pulley 34 that carries out the belt transmission by the belt 33 are composed; Drive the dynamic pressure spool frame 43 for rotational movement, the constant pressure spool frame 44 corresponding to the position of the dynamic pressure spool frame 43, the wire pas...
PUM
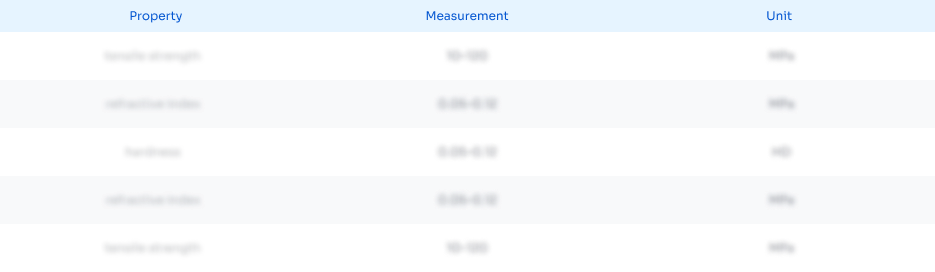
Abstract
Description
Claims
Application Information

- Generate Ideas
- Intellectual Property
- Life Sciences
- Materials
- Tech Scout
- Unparalleled Data Quality
- Higher Quality Content
- 60% Fewer Hallucinations
Browse by: Latest US Patents, China's latest patents, Technical Efficacy Thesaurus, Application Domain, Technology Topic, Popular Technical Reports.
© 2025 PatSnap. All rights reserved.Legal|Privacy policy|Modern Slavery Act Transparency Statement|Sitemap|About US| Contact US: help@patsnap.com