Clamp used for water cutting of side frame casting of railway wagon
A railway freight car and water jet cutting technology, which is applied in the field of machining, can solve the problems of the side frame casting riser being harmful, polluting the environment, and the side frame casting being unable to achieve stable positioning.
- Summary
- Abstract
- Description
- Claims
- Application Information
AI Technical Summary
Problems solved by technology
Method used
Image
Examples
specific Embodiment approach 1
[0019] Specific implementation mode one: combine figure 1 , figure 2 , image 3 , Figure 4 , Figure 5 with Image 6 Describe this embodiment. This embodiment includes a support base 1, a first positioning block 2, a second positioning block 3, a pressure wheel member 4, a pressing rod 5 and a connecting rod 6. There are three The first positioning nail 7, the top surface of the support base 1 is a three-nail positioning surface C' matched with the positioning surface C of the bottom surface of the side frame casting, and the three-nail positioning surface C' is sequentially provided with first The positioning block 2, the second positioning block 3 and the connecting rod 6, the gap between the first positioning block 2 and the second positioning block 3 is set, the first positioning block 2 is a rectangular block, and one side of the first positioning block 2 There are two second positioning nails 8 arranged side by side. One side of the first positioning block 2 is a ...
specific Embodiment approach 2
[0022] Specific implementation mode two: combination image 3 with Figure 4 To illustrate this embodiment, in this embodiment, the three first positioning nails 7 surround and form a triangular positioning surface, and the first positioning block 2 is located on the triangular positioning surface.
[0023] The location of the first positioning block 2 on the triangular positioning surface is specifically set for the structure of the bottom surface of the side frame casting, so that the positioning effect of the first positioning block 2 on the bottom surface of the side frame casting is more accurate. Other unmentioned structures and connections are the same as those in the first embodiment.
specific Embodiment approach 3
[0024] Specific implementation mode three: combination image 3 Describe this embodiment, the pressure wheel part 4 in this embodiment includes a pressure plate 4-1 and a roller 4-2, the pressure plate 4-1 is arranged in parallel with the connecting rod 6, and the lower end of the pressure plate 4-1 is provided with a roller 4-2. 2. The roller 4-2 rolls on the side of the second positioning block 3 opposite to the first positioning block 2, and the upper end of the pressing plate 4-1 is hinged to one end of the pressing rod 5. Other unmentioned structures and connections are the same as those in the first or second embodiment.
PUM
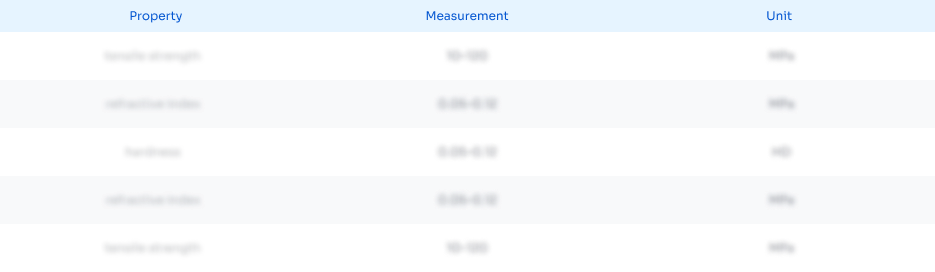
Abstract
Description
Claims
Application Information

- Generate Ideas
- Intellectual Property
- Life Sciences
- Materials
- Tech Scout
- Unparalleled Data Quality
- Higher Quality Content
- 60% Fewer Hallucinations
Browse by: Latest US Patents, China's latest patents, Technical Efficacy Thesaurus, Application Domain, Technology Topic, Popular Technical Reports.
© 2025 PatSnap. All rights reserved.Legal|Privacy policy|Modern Slavery Act Transparency Statement|Sitemap|About US| Contact US: help@patsnap.com