Fuel jetting mixing device and low-pressure fuel jetting mixing method in supersonic velocity flow field
A technology of fuel injection and supersonic flow, which is applied in the field of low-pressure injection and mixing of fuel in supersonic flow field and fuel injection and mixing device in supersonic flow field, and can solve the problem of high injection pressure requirements, low penetration depth and poor mixing effect. and other problems, to achieve the effect of good mixing effect, increasing penetration depth and reducing working pressure
- Summary
- Abstract
- Description
- Claims
- Application Information
AI Technical Summary
Problems solved by technology
Method used
Image
Examples
Embodiment Construction
[0025] The embodiments of the present invention will be described in detail below with reference to the accompanying drawings, but the present invention can be implemented in various ways defined and covered.
[0026] figure 1 It is a schematic diagram of the working principle of the fuel injection mixing device in the supersonic flow field of the preferred embodiment of the present invention; figure 2 yes figure 1 Schematic diagram of the structure of the fuel chamber and the injection hole; image 3 yes figure 1 Schematic diagram of the structure of the vortex generator in ; Figure 4 It is a schematic flow chart of a fuel low-pressure injection mixing method in a supersonic flow field according to a preferred embodiment of the present invention.
[0027] Such as figure 1As shown, the fuel injection and mixing device in the supersonic flow field of this embodiment includes: a fuel supply system for injecting gaseous fuel 2 into the high-speed main flow 6 in the superso...
PUM
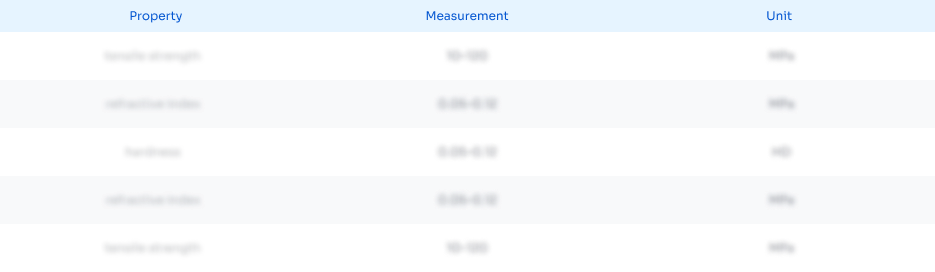
Abstract
Description
Claims
Application Information

- R&D Engineer
- R&D Manager
- IP Professional
- Industry Leading Data Capabilities
- Powerful AI technology
- Patent DNA Extraction
Browse by: Latest US Patents, China's latest patents, Technical Efficacy Thesaurus, Application Domain, Technology Topic, Popular Technical Reports.
© 2024 PatSnap. All rights reserved.Legal|Privacy policy|Modern Slavery Act Transparency Statement|Sitemap|About US| Contact US: help@patsnap.com