Calibration method for synthesizing far field through single detector to improve double-beam synthesis precision and pointing accuracy
A technology with single detector and synthetic precision, which is applied in the field of optical engineering, can solve problems such as unrealistic and large detector dimensions, and achieve the effects of ensuring identity, avoiding thermal drift, and ensuring closed-loop accuracy
- Summary
- Abstract
- Description
- Claims
- Application Information
AI Technical Summary
Problems solved by technology
Method used
Image
Examples
Embodiment Construction
[0026] The present invention will be described in detail below in conjunction with the accompanying drawings and specific embodiments.
[0027] Such as figure 1 The first beam of light emitted by the first laser 1-9 shown passes through the first tunable mirror 1-1, the first transmission mirror 1-2, the second transmission mirror 1-3, and then synthesizes the beam-splitting and combining mirror 1-4. The second beam of light emitted by the second laser 1-10 passes through the second tunable mirror 1-5 and the third transmission mirror 1-6 and enters the composite beam-splitting mirror 1-4. Most of the energy of the first beam of light is reflected as the main beam through the composite beam-splitter mirror 1-4, and a very small part of the energy is transmitted into the composite sensor 1-11 through the composite beam-splitter mirror 1-4 as the measurement beam; the second beam of light Most of the energy is transmitted as the main beam through the composite beam-splitting mi...
PUM
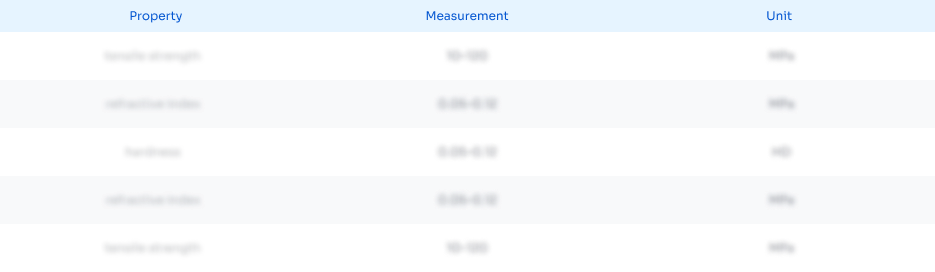
Abstract
Description
Claims
Application Information

- R&D
- Intellectual Property
- Life Sciences
- Materials
- Tech Scout
- Unparalleled Data Quality
- Higher Quality Content
- 60% Fewer Hallucinations
Browse by: Latest US Patents, China's latest patents, Technical Efficacy Thesaurus, Application Domain, Technology Topic, Popular Technical Reports.
© 2025 PatSnap. All rights reserved.Legal|Privacy policy|Modern Slavery Act Transparency Statement|Sitemap|About US| Contact US: help@patsnap.com