Die-free fast casting method based on fused deposition technology
A rapid casting and fused deposition technology, applied in casting molding equipment, tools, molds, etc., can solve the problems of high production cost, high price, difficult equipment use and maintenance, etc., and achieve high precision and good flexibility.
- Summary
- Abstract
- Description
- Claims
- Application Information
AI Technical Summary
Problems solved by technology
Method used
Image
Examples
Embodiment 1
[0038] Using this method to cast the reducer housing, the material is HT200, the outline size is 318mm×268mm×225mm, and the minimum wall thickness is 6mm.
[0039] It is a metal moldless rapid casting method, comprising the following steps:
[0040] Step 1 Preparation of Ceramic-Plastic Mixed Filament
[0041] Mix 500 mesh clay fine powder and 500 mesh ABS plastic powder evenly to obtain a mixture of clay fine powder and ABS plastic powder. In the mixture, the clay fine powder accounts for 50%, and the mixture is extruded into a diameter of 1.75 with a plastic extruder. ±0.03mm filament coil 6;
[0042] Step 2 Prepare the 3D CAD data of the casting shell
[0043] Use 3D CAD software to convert the 3D solid model of the part to be cast into a shell model and enlarge it by 1.22 times, set the sprue shell 13 and the riser shell 9 on the enlarged 3D shell model, and set the sprue shell 13 And the three-dimensional shell model data of riser shell 9 is converted into the STL data...
Embodiment 2
[0055] The pump body of the gear pump is cast by this method, and its material is cast aluminum ZL104, the outline size is 220mm×128mm×225mm, and the minimum wall thickness is 15mm.
[0056] It is a metal moldless rapid casting method, comprising the following steps:
[0057] Step 1 Preparation of Ceramic-Plastic Mixed Filament
[0058] Mix 800-mesh china clay micro-powder and 800-mesh PLA plastic powder evenly to obtain a mixture of china clay micro-powder and PLA plastic powder. In the mixture, the china clay micro-powder accounts for 65%, and use a plastic extruder to extrude the mixture into a diameter of 3 ±0.05mm filament coil 6;
[0059] Step 2 Prepare the 3D CAD data of the casting shell
[0060] Use 3D CAD software to convert the 3D solid model of the part to be cast into a shell model and enlarge it by 1.182 times, set the sprue shell 13 and the riser shell 9 on the enlarged 3D shell model, and set the sprue shell 13 And the three-dimensional shell model data of r...
Embodiment 3
[0072] The valve body is cast by this method, the material is malleable cast iron KTH300-06, the outline size is 210mm×210mm×125mm, and the minimum wall thickness is 12mm.
[0073] It is a metal moldless rapid casting method, comprising the following steps:
[0074] Step 1 Preparation of Ceramic-Plastic Mixed Filament
[0075] Mix 1200-mesh kaolin powder with 1200-mesh ABS plastic powder evenly to obtain a mixture of kaolin powder and ABS plastic powder. In the mixture, the proportion of kaolin powder is 45%. Use a plastic extruder to extrude the mixture into a diameter of 1.75 ±0.03mm filament coil 6;
[0076] Step 2 Prepare the 3D CAD data of the casting shell
[0077] Use 3D CAD software to convert the 3D solid model of the part to be cast into a shell model and enlarge it by 1.26 times, set the sprue shell 13 and the riser shell 9 on the enlarged 3D shell model, and set the sprue shell 13 And the three-dimensional shell model data of riser shell 9 is converted into the ...
PUM
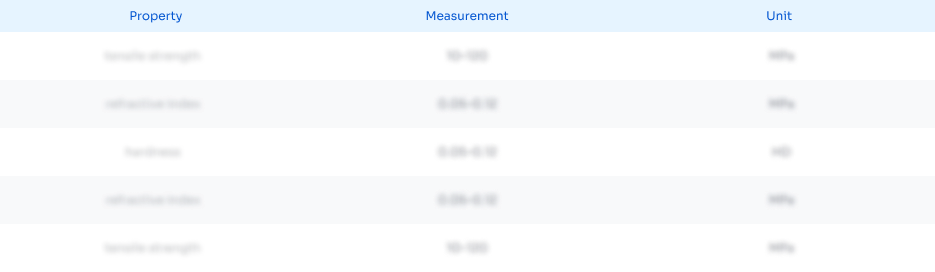
Abstract
Description
Claims
Application Information

- R&D
- Intellectual Property
- Life Sciences
- Materials
- Tech Scout
- Unparalleled Data Quality
- Higher Quality Content
- 60% Fewer Hallucinations
Browse by: Latest US Patents, China's latest patents, Technical Efficacy Thesaurus, Application Domain, Technology Topic, Popular Technical Reports.
© 2025 PatSnap. All rights reserved.Legal|Privacy policy|Modern Slavery Act Transparency Statement|Sitemap|About US| Contact US: help@patsnap.com