An overflow ball mill with wedge-shaped liner plate structure and its liner plate installation method
A ball mill and overflow-type technology, which is applied in the field of large-scale overflow ball mill structure, can solve the problems of affecting the environmental sanitation of the mill, easy loosening of the through-hole liner, and high manual labor intensity, etc., and achieves scientific and effective installation methods and lightens the operation. The effect of safety and labor intensity reduction
- Summary
- Abstract
- Description
- Claims
- Application Information
AI Technical Summary
Problems solved by technology
Method used
Image
Examples
Embodiment Construction
[0022] Such as figure 1 , figure 2 As shown, the present invention includes a ball mill barrel 1, end caps 2 at both ends of the barrel, a rubber pad cushion 3 installed in the barrel, a barrel liner 4, and an end cover liner 5 installed in the end cap. The barrel liner 4 is a wedge-shaped liner with beveled surfaces at both ends and a raised arc surface on the inner surface, and a reverse wedge pressed into the bevel is used between two adjacent barrel liners. The key-shaped bead 6 is pressed tightly, and the connecting bolt 7 passes through the bead from the inside of the cylinder body 1 and passes through the cylinder body, and a nut is taken from the outside of the cylinder body to install the cylinder liner firmly. The beveled surface of the barrel liner at both ends fits and locks with the end bevel of the end cover liner. The end cover liner 5 is mounted on the end cover 2 by connecting bolts 8 . Countersunk holes are processed on the wedge-shaped bead 6, and the co...
PUM
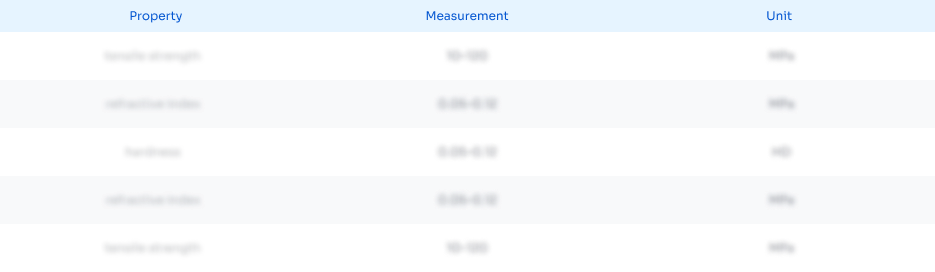
Abstract
Description
Claims
Application Information

- Generate Ideas
- Intellectual Property
- Life Sciences
- Materials
- Tech Scout
- Unparalleled Data Quality
- Higher Quality Content
- 60% Fewer Hallucinations
Browse by: Latest US Patents, China's latest patents, Technical Efficacy Thesaurus, Application Domain, Technology Topic, Popular Technical Reports.
© 2025 PatSnap. All rights reserved.Legal|Privacy policy|Modern Slavery Act Transparency Statement|Sitemap|About US| Contact US: help@patsnap.com