Machining method for hollow shaft
A processing method and hollow shaft technology, applied in metal processing, metal processing equipment, manufacturing tools, etc., can solve problems such as low efficiency and poor practical effect, and achieve good practical effect
- Summary
- Abstract
- Description
- Claims
- Application Information
AI Technical Summary
Problems solved by technology
Method used
Examples
Embodiment 1
[0007] The invention includes: loading the rough material into a machining center, turning it, peeling it, and processing it into a standard bar material. Put the standard bar stock into the milling machine under the condition of oil cooling, mill out the standard surface, put the bar stock vertically into the machining center, define the reference plane, and place the bar stock under the condition of oil cooling and inert gas protection The center of the material is hollowed out, and the outer surface is processed into various sizes of outer diameters. Note that certain chamfers are reserved between the various outer diameters to prevent structural stress. When the two ends of the bar are sealed, attention should be paid to the use of interference fit components, hydraulic assembly, and precise flaw detection after assembly. Prevent the damage in the process of assembly machining from entering the next process without being found, causing the shaft to break easily.
Embodiment 2
[0009] The invention includes: loading the blank into a machining center, turning it, peeling it off, and processing it into a standard bar. Put the standard bar stock into the milling machine under the condition of oil cooling, mill out the standard surface, put the bar stock vertically into the machining center, define the reference plane, and place the bar stock under the condition of oil cooling and inert gas protection The center of the material is hollowed out, and the outer surface is processed into various sizes of outer diameters. Note that certain chamfers are reserved between the various outer diameters to prevent structural stress. When the two ends of the bar are sealed, attention should be paid to the use of interference fit components, hydraulic assembly, and precise flaw detection after assembly. Prevent the damage in the process of assembly machining from entering the next process without being found, causing the shaft to break easily.
Embodiment 3
[0011] The invention includes: loading the blank into a machining center, turning it, peeling it off, and processing it into a standard bar. Put the standard bar stock into the milling machine under the condition of oil cooling, mill out the standard surface, put the bar stock vertically into the machining center, define the reference plane, and place the bar stock under the condition of oil cooling and inert gas protection The center of the material is hollowed out, and the outer surface is processed into various sizes of outer diameters. Note that certain chamfers are reserved between the various outer diameters to prevent structural stress. When the two ends of the bar are sealed, attention should be paid to the use of interference fit components, hydraulic assembly, and precise flaw detection after assembly. Prevent the damage in the process of assembly machining from entering the next process without being found, causing the shaft to break easily.
PUM
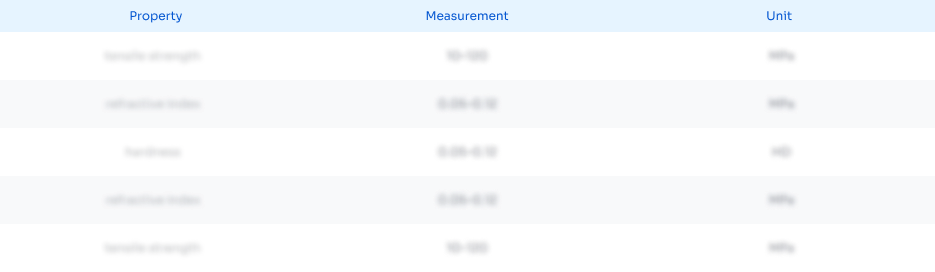
Abstract
Description
Claims
Application Information

- R&D
- Intellectual Property
- Life Sciences
- Materials
- Tech Scout
- Unparalleled Data Quality
- Higher Quality Content
- 60% Fewer Hallucinations
Browse by: Latest US Patents, China's latest patents, Technical Efficacy Thesaurus, Application Domain, Technology Topic, Popular Technical Reports.
© 2025 PatSnap. All rights reserved.Legal|Privacy policy|Modern Slavery Act Transparency Statement|Sitemap|About US| Contact US: help@patsnap.com