Welding spot arrangement optimization method based on welding spot force-bearing homogenization
A technology of uniform force and optimization method, applied in special data processing applications, instruments, electrical digital data processing, etc., can solve the problem of lack of solder joint layout design method, and achieve the purpose of reducing welding cost, number and failure. Effect
- Summary
- Abstract
- Description
- Claims
- Application Information
AI Technical Summary
Problems solved by technology
Method used
Image
Examples
Embodiment Construction
[0030] The present invention will be described in further detail below in conjunction with the accompanying drawings and specific embodiments.
[0031] The solder joint arrangement optimization method based on the uniform stress of the solder joints in the present invention is based on the structure topology optimization design technology, and the purpose is to make the stress distribution of each solder joint in the optimized solder joint arrangement form uniform, and ensure the dynamic and static strength of the welding structure. Under the conditions of rigidity and rigidity, it can effectively reduce the failure of solder joints in the load-bearing process, reduce the number of solder joints, and reduce welding costs.
[0032] The main design idea of the solder joint arrangement optimization method based on the uniform stress of the solder joints in the present invention includes:
[0033] (1) Establish a finite element model of the initial welded structure containing mu...
PUM
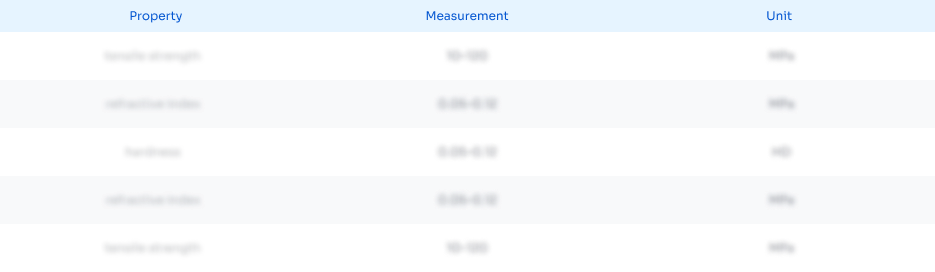
Abstract
Description
Claims
Application Information

- R&D
- Intellectual Property
- Life Sciences
- Materials
- Tech Scout
- Unparalleled Data Quality
- Higher Quality Content
- 60% Fewer Hallucinations
Browse by: Latest US Patents, China's latest patents, Technical Efficacy Thesaurus, Application Domain, Technology Topic, Popular Technical Reports.
© 2025 PatSnap. All rights reserved.Legal|Privacy policy|Modern Slavery Act Transparency Statement|Sitemap|About US| Contact US: help@patsnap.com