High-magnitude axial compression and binding joint load realization device
A combined load, high-level technology, used in the testing of measuring devices, instruments, and mechanical components, can solve the problem of easy interference between the loading device and the frame structure, and achieve the effect of overcoming self-weight.
- Summary
- Abstract
- Description
- Claims
- Application Information
AI Technical Summary
Problems solved by technology
Method used
Image
Examples
Embodiment Construction
[0028] The present invention will be described in detail below in conjunction with the accompanying drawings and specific embodiments.
[0029] Such as image 3 — Figure 5 As shown, the high-level axial compression and binding combined load realization device of the present invention includes four 12m high-strength beams 1, 18 supporting column blocks 2, 8 corner braces 3, eight 1m column blocks 4, two 7m high-strength beams 5, 14 load application devices 6, two high-strength column beams 7, 1 load-bearing steel frame 8, 1 test platform 9, 8 fixed beams 10, 2 bearing walls 11, 2 sides Top column block 12, 4 loading angle braces 13, 4 loading beams 14, 4 tie rods 15, 2 fixing square plates 16, 1 fixing ring 17 and transition tooling 19; The force gauge and the connecting rod are connected by threads;
[0030] Axial compression load realization device connection relationship: the combined test piece 18 includes, from top to bottom, the first-level engine frame, the first-lev...
PUM
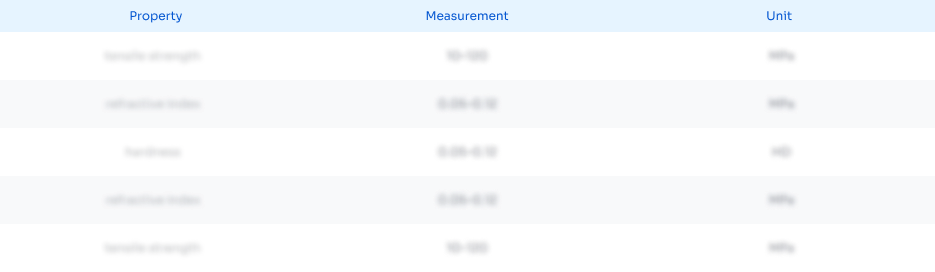
Abstract
Description
Claims
Application Information

- R&D
- Intellectual Property
- Life Sciences
- Materials
- Tech Scout
- Unparalleled Data Quality
- Higher Quality Content
- 60% Fewer Hallucinations
Browse by: Latest US Patents, China's latest patents, Technical Efficacy Thesaurus, Application Domain, Technology Topic, Popular Technical Reports.
© 2025 PatSnap. All rights reserved.Legal|Privacy policy|Modern Slavery Act Transparency Statement|Sitemap|About US| Contact US: help@patsnap.com