Crack detection tool for metal plate stamping
A crack detection and tooling technology, which is applied in metal processing, metal processing equipment, manufacturing tools, etc., can solve the problems of low reliability, lack of detection devices, cracks in bending places and stretched surfaces, etc., and achieve comprehensive detection , The effect of reliability improvement
- Summary
- Abstract
- Description
- Claims
- Application Information
AI Technical Summary
Problems solved by technology
Method used
Image
Examples
Embodiment Construction
[0010] The specific embodiments of the present invention will be further described below in conjunction with the accompanying drawings.
[0011] Such as figure 1 As shown, in the crack detection tool for sheet metal stamping in this embodiment, the sheet metal part 1 is installed horizontally on the stamping support seat 2, the stamping head 3 is placed above it, and the stamping die 4 is installed below it. Cavity 401, located between the stamping head 3 and the sheet metal part 1, is provided with an ultrasonic crack detection head 5 for detecting bends. There is an escape through hole 501 larger than the outer diameter of the stamping head 3 , and its periphery is an ultrasonic detection ring 502 .
[0012] The invention uses an ultrasonic crack detection head to detect the sheet metal parts in the stamping process, and detects the bending part without later detection, and compared with the naked eye detection, the detection is comprehensive and the reliability is greatly ...
PUM
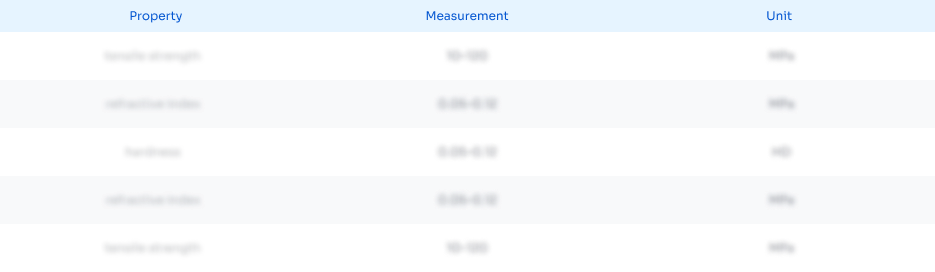
Abstract
Description
Claims
Application Information

- R&D Engineer
- R&D Manager
- IP Professional
- Industry Leading Data Capabilities
- Powerful AI technology
- Patent DNA Extraction
Browse by: Latest US Patents, China's latest patents, Technical Efficacy Thesaurus, Application Domain, Technology Topic, Popular Technical Reports.
© 2024 PatSnap. All rights reserved.Legal|Privacy policy|Modern Slavery Act Transparency Statement|Sitemap|About US| Contact US: help@patsnap.com