Polyurethane transparent skin material and preparing method thereof
A skin material, polyurethane technology, applied in the field of polyurethane products, can solve the problems of difficult operation, high hardness, high temperature processing, etc., and achieve the effect of convenient and simple operation, high toughness and high transparency
- Summary
- Abstract
- Description
- Claims
- Application Information
AI Technical Summary
Problems solved by technology
Method used
Image
Examples
Embodiment 1
[0029] The composition of raw materials is as follows:
[0030] A component:
[0031] Polyether polyol DDL-4000D60kg
[0032] Polyisocyanate T-1005kg;
[0033] B component:
[0034] Polyether polyol DDL-3000D10kg
[0035] Ultraviolet absorber UV-5310.01kg
[0036] Diethyltoluenediamine 6kg.
[0037] The preparation method is as follows:
[0038] (1) Preparation of component A: Heat polyether polyol DDL-4000D to 110°C for 2 hours in vacuum dehydration, cool down to below 50°C and add polyisocyanate, heat up to 80°C and react for 2 hours to obtain a prepolymer. The NCO% of the polymer is 2%, the temperature is lowered to below 50°C, stirred evenly, and sealed for later use;
[0039] (2) Preparation of component B: Mix and stir polyether polyol DDL-3000D, ultraviolet absorber and diethyltoluenediamine for 20 minutes and seal it for later use;
[0040] (3) Mix and stir components A and B for 10 seconds, then pour them into a mold coated with a release agent, heat and press...
Embodiment 2
[0045] The composition of raw materials is as follows:
[0046] A component:
[0047] Polyether polyol DDL-4000D90kg
[0048] Polyisocyanate T-100 20kg;
[0049] B component:
[0050] Polyether polyol DDL-3000D50kg
[0051] Ultraviolet absorber UV-5310.2kg
[0052] Diethyltoluenediamine 20kg.
[0053] The preparation method is as follows:
[0054] (1) Preparation of component A: heat up polyether polyol DDL-4000D to 120°C for 2.5 hours in vacuum dehydration, cool down to below 50°C and add polyisocyanate, heat up to 85°C and react for 3 hours to obtain a prepolymer. The NCO% of the polymer is 7%, the temperature is lowered to below 50°C, stirred evenly, and sealed for later use;
[0055] (2) Preparation of component B: Mix and stir polyether polyol DDL-3000D, ultraviolet absorber and diethyltoluenediamine for 25 minutes and seal it for later use;
[0056] (3) Mix and stir components A and B for 15 seconds, then pour them into a mold coated with release agent, heat and ...
Embodiment 3
[0061] The composition of raw materials is as follows:
[0062] A component:
[0063] Polyether polyol DDL-4000D80kg
[0064] Polyisocyanate T-100 10kg;
[0065] B component:
[0066] Polyether polyol DDL-3000D30kg
[0067] Ultraviolet absorber UV-5310.1kg
[0068] Diethyltoluenediamine 10kg.
[0069] The preparation method is as follows:
[0070] (1) Preparation of component A: heat up polyether polyol DDL-4000D to 115°C for 2.3 hours in vacuum dehydration, cool down to below 50°C and add polyisocyanate, heat up to 82°C and react for 2.5 hours to obtain a prepolymer. The NCO% of the polymer is 5%, and the temperature is lowered to below 50°C, stirred evenly, and sealed for later use;
[0071] (2) Preparation of component B: Mix and stir polyether polyol DDL-3000D, ultraviolet absorber and diethyltoluenediamine for 23 minutes and seal it for later use;
[0072] (3) Mix and stir components A and B for 12 seconds, then pour them into a mold coated with release agent, hea...
PUM
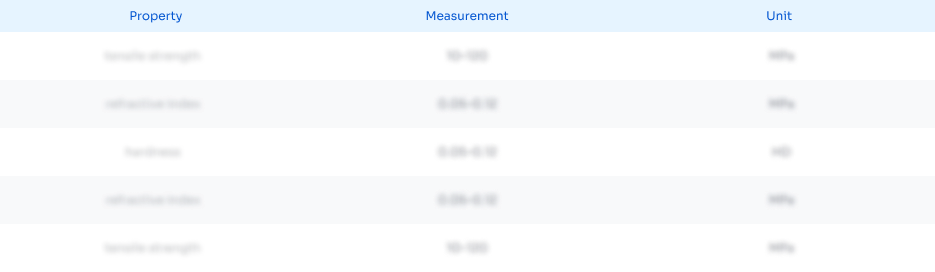
Abstract
Description
Claims
Application Information

- Generate Ideas
- Intellectual Property
- Life Sciences
- Materials
- Tech Scout
- Unparalleled Data Quality
- Higher Quality Content
- 60% Fewer Hallucinations
Browse by: Latest US Patents, China's latest patents, Technical Efficacy Thesaurus, Application Domain, Technology Topic, Popular Technical Reports.
© 2025 PatSnap. All rights reserved.Legal|Privacy policy|Modern Slavery Act Transparency Statement|Sitemap|About US| Contact US: help@patsnap.com