A kind of preparation technology of copper-clad aluminum composite V-shaped wire
A preparation process, copper-clad aluminum technology, applied in the direction of cable/conductor manufacturing, electrical components, circuits, etc., can solve the problems of complex process, low bonding strength, large equipment investment, etc., and achieve high dimensional accuracy, high bonding strength, and process high efficiency effect
- Summary
- Abstract
- Description
- Claims
- Application Information
AI Technical Summary
Problems solved by technology
Method used
Image
Examples
Embodiment Construction
[0017] For better understanding and implementation, the present invention will be further described below in conjunction with accompanying drawing:
[0018] A preparation process for a copper-clad aluminum composite V-shaped wire. First, the core aluminum and the cladding layer copper are composited into a copper-clad aluminum composite body. The blank is made by a direct composite forming method of horizontal continuous casting. The area ratio of the cladding copper layer About 30%, including the following steps:
[0019] (1) Rolling: For billets with a square section with corners, the blanking method: the size of the billet is about 44mm×44mm, rolling with a pass, the rolling speed is about 40m / min, the first three passes, in order rolling, vertical rolling, and flat rolling, with a reduction of about 30%; the middle three passes are vertical rolling, flat rolling, and vertical rolling with a deformation of about 15%; followed by flat rolling, vertical rolling, and a reducti...
PUM
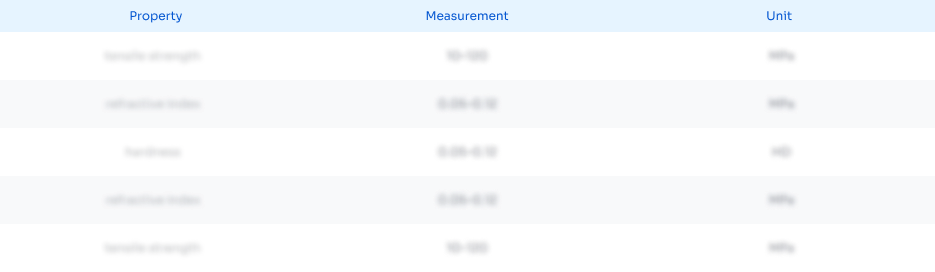
Abstract
Description
Claims
Application Information

- R&D Engineer
- R&D Manager
- IP Professional
- Industry Leading Data Capabilities
- Powerful AI technology
- Patent DNA Extraction
Browse by: Latest US Patents, China's latest patents, Technical Efficacy Thesaurus, Application Domain, Technology Topic, Popular Technical Reports.
© 2024 PatSnap. All rights reserved.Legal|Privacy policy|Modern Slavery Act Transparency Statement|Sitemap|About US| Contact US: help@patsnap.com