Motorized spindle structure optimization method based on parametric finite element model
An optimization method, the technology of the electric spindle, applied in the direction of electric digital data processing, special data processing applications, instruments, etc., can solve the problem of not considering high rigidity and light weight at the same time, not being able to optimize the structure of the electric spindle, and not being able to describe the actual situation of the spindle well and other problems, to achieve the effect of accurate model and obvious optimization effect
- Summary
- Abstract
- Description
- Claims
- Application Information
AI Technical Summary
Problems solved by technology
Method used
Image
Examples
Embodiment 1
[0048] refer to figure 2, Optimal design of U25-215446 milling electric spindle, which is used for high-speed milling of CNC machine tools, and can be used for semi-finishing and finishing. Specifically follow the steps below to optimize the motorized spindle:
[0049] First, according to the object to be optimized, the optimized design variables and optimization objectives are defined in advance. Depend on figure 2 It can be seen that the electric spindle is composed of three bearings (respectively image 3 4, 5, 6) in the support. The front end is installed by a pair of angular contact ball bearings back to back, and there is a certain span between the two bearings; the rear end is supported by a floating displacement bearing to bear radial load. When optimizing the structure, refer to image 3 , select the main shaft overhang a, the front end bearing span L 1 , Back end bearing span L 2 And the outer diameter D of the rear end is the design variable, and the optimi...
Embodiment 2
[0091] refer to Figure 4 , an optimized design of a large-scale high-precision CNC form grinding electromechanical spindle. This electric spindle is used in CNC profile gear grinding machine for precision machining of large gears. Specifically follow the steps below to optimize the motorized spindle:
[0092] First, according to the object to be optimized, the optimized design variables and optimization objectives are defined in advance. From Figure 4 It can be seen that the front end of the electric spindle consists of 4 angular contact ball bearings installed back to back in pairs (corresponding to Figure 5 Combination bearings 4', 5'); the rear end is supported by two angular contact ball bearings to form a pair of back-to-back installation (corresponding Figure 5 Combined bearing 6'). refer to Figure 5 , when the structure is optimized, select the main shaft overhang a, the front end bearing span L 1 , Back end bearing span L 2 , front end shaft diameter D 1 ...
PUM
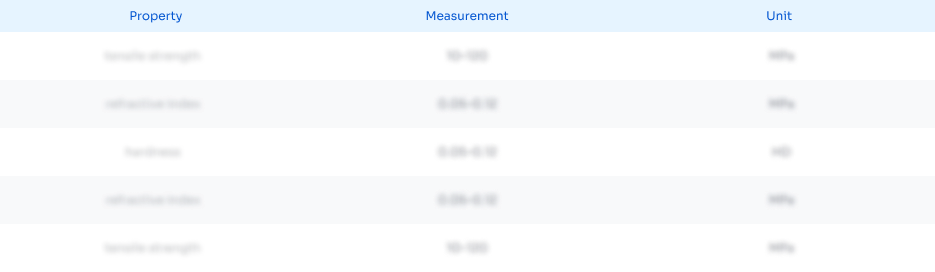
Abstract
Description
Claims
Application Information

- R&D
- Intellectual Property
- Life Sciences
- Materials
- Tech Scout
- Unparalleled Data Quality
- Higher Quality Content
- 60% Fewer Hallucinations
Browse by: Latest US Patents, China's latest patents, Technical Efficacy Thesaurus, Application Domain, Technology Topic, Popular Technical Reports.
© 2025 PatSnap. All rights reserved.Legal|Privacy policy|Modern Slavery Act Transparency Statement|Sitemap|About US| Contact US: help@patsnap.com