Natural gas thermal treatment furnace
A heat treatment furnace, natural gas technology, applied in the direction of waste heat treatment, furnace, furnace type, etc., can solve the problems of uneven heating, high cost, increased energy consumption, etc., achieve good heat insulation performance, long service life, and reduce consumption Effect
- Summary
- Abstract
- Description
- Claims
- Application Information
AI Technical Summary
Problems solved by technology
Method used
Image
Examples
Embodiment Construction
[0023] Such as Figure 1-Figure 2 As shown, the natural gas heat treatment furnace includes a furnace body 1, a furnace door 3 is provided on the front side of the furnace body 1, a horizontal guide rail 2 is provided at the bottom of the furnace body 1, the horizontal guide rail 2 extends to the outside of the furnace body, and a trolley is provided on the guide rail 2 4. Refractory parts are laid on the trolley 4; three flue openings 8 are evenly arranged on the side wall of the bottom of the furnace body 1; Three flue openings are set, which overcomes the overheating defect of the side flue openings.
[0024] An air displacer 9 is arranged in the flue at the bottom of the furnace body 1, and the intake pipe 13 of the air displacer 9 is used for cold air to enter. The outlet pipeline 14 of the air displacer 9 is connected to the burner 11 at the side of the furnace body 1 . The air outlet pipeline 14 that the air displacer 9 communicates with the burner 11 is also connecte...
PUM
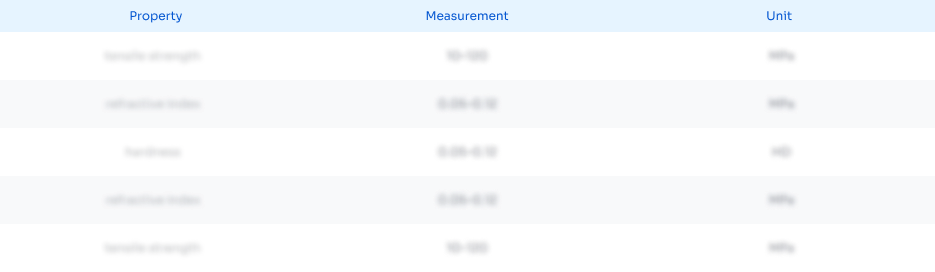
Abstract
Description
Claims
Application Information

- R&D
- Intellectual Property
- Life Sciences
- Materials
- Tech Scout
- Unparalleled Data Quality
- Higher Quality Content
- 60% Fewer Hallucinations
Browse by: Latest US Patents, China's latest patents, Technical Efficacy Thesaurus, Application Domain, Technology Topic, Popular Technical Reports.
© 2025 PatSnap. All rights reserved.Legal|Privacy policy|Modern Slavery Act Transparency Statement|Sitemap|About US| Contact US: help@patsnap.com