Manufacturing technology for bent LED filament and bulb with bent LED filament
A technology of LED filament and manufacturing process, which is applied to the components of lighting devices, semiconductor devices of light-emitting elements, lighting devices, etc., and can solve problems such as difficulty in making various curved shapes
- Summary
- Abstract
- Description
- Claims
- Application Information
AI Technical Summary
Problems solved by technology
Method used
Image
Examples
Embodiment Construction
[0031] The present invention will be described in further detail below in conjunction with the accompanying drawings and specific embodiments.
[0032] The present invention firstly discloses the manufacturing process of curved LED filament, including the following steps:
[0033] (1) On a piece of flexible metal plate or resin plate, use a circuit drawing machine to describe a spiral circuit; the flexible metal plate mentioned in the present invention can be any metal material plate with flexible characteristics;
[0034] (2) Die-bonding is performed on the front and back sides of the spiral circuit that has been drawn; the die-bonding mentioned in the present invention is also called DieBond or chip mounting, and the die-bonding is through colloid (generally conductive for LEDs). glue or insulating glue) to bond the chip to the designated area of the bracket to form a thermal path or an electrical path, which provides conditions for the subsequent wiring connection.
[00...
PUM
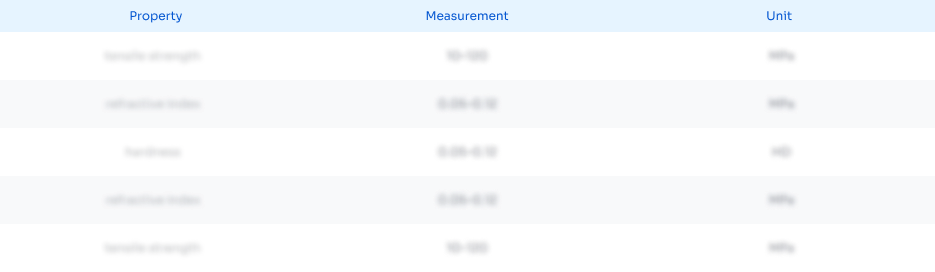
Abstract
Description
Claims
Application Information

- R&D Engineer
- R&D Manager
- IP Professional
- Industry Leading Data Capabilities
- Powerful AI technology
- Patent DNA Extraction
Browse by: Latest US Patents, China's latest patents, Technical Efficacy Thesaurus, Application Domain, Technology Topic, Popular Technical Reports.
© 2024 PatSnap. All rights reserved.Legal|Privacy policy|Modern Slavery Act Transparency Statement|Sitemap|About US| Contact US: help@patsnap.com