Phosphorus-nitrogen nano flame retardant of core-shell structure and preparation method thereof
A nano flame retardant, core-shell structure technology, applied in the field of flame retardants, can solve the problems of destroying the structure and properties of carbon nanotubes, harsh reaction conditions, etc., and achieve the effect of obvious flame retardant effect, low equipment requirements, and less waste.
- Summary
- Abstract
- Description
- Claims
- Application Information
AI Technical Summary
Problems solved by technology
Method used
Image
Examples
Embodiment 1
[0026] Add 1.00g of carbon nanotubes and 3.09g of triethylamine into a three-necked flask containing 200mL of xylene, pre-disperse for 120min under the action of 200W ultrasonic waves; add 2.48g of phenylphosphonic acid dichloride, stir evenly, and maintain the reaction system At a temperature of 0°C, add 3.02g of 4,4'-diaminodiphenylmethane in 50mL of xylene solution dropwise. After the dropwise addition, raise the temperature of the reaction system to 60°C for 12 hours; filter the reaction mixture with suction, and then use two Wash 3 times with toluene, and then wash 3 times with deionized water, and dry the obtained solid product under vacuum at 80°C to constant weight to obtain a core-shell structure phosphorus-nitrogen nano-flame retardant with a yield of 90.4%. The layer quality fraction is 77.1%.
Embodiment 2
[0028] Add 1.00g of carbon nanotubes and 6.18g of triethylamine into a three-necked flask containing 240mL of tetrahydrofuran, and pre-disperse for 90 minutes under the action of 250W ultrasound; add 4.96g of phenylphosphonic acid dichloride, stir well, and maintain the temperature of the reaction system to 5°C, add 6.05g of 4,4'-diaminodiphenylmethane in 60mL tetrahydrofuran solution dropwise. After the dropwise addition, raise the temperature of the reaction system to 50°C for 10 hours; filter the reaction mixture with suction, and then wash it with tetrahydrofuran for 3 times, and then washed 4 times with deionized water, and the resulting solid product was dried to constant weight under vacuum at 70°C to obtain a core-shell structure phosphorus-nitrogen nano-flame retardant, with a yield of 85.7%, and the shell mass fraction was 80.8%.
Embodiment 3
[0030] Add 1.00g of carbon nanotubes and 12.95g of sodium carbonate into a three-necked flask filled with 300mL of acetone, and pre-disperse for 60 minutes under the action of 300W ultrasound; -5°C, add 12.10g of 4,4'-diaminodiphenylmethane in 70mL of acetone solution dropwise. After the dropwise addition, raise the temperature of the reaction system to 45°C for 14 hours; filter the reaction mixture with suction, and then wash it with acetone for 3 times, and then washed 3 times with deionized water, and the resulting solid product was dried to constant weight under vacuum at 75°C to obtain a core-shell structure phosphorus-nitrogen nano-flame retardant with a yield of 86.2%, and the shell mass fraction was 92.7%.
PUM
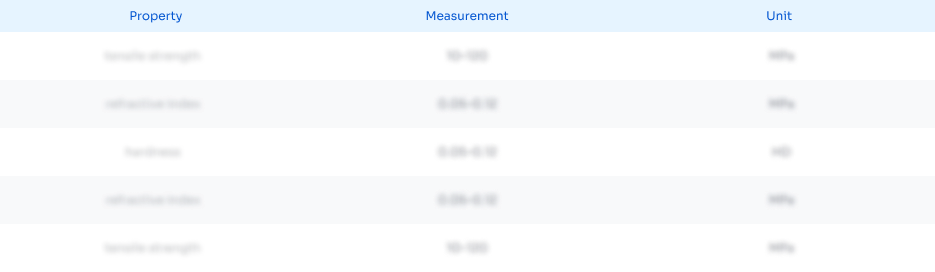
Abstract
Description
Claims
Application Information

- R&D
- Intellectual Property
- Life Sciences
- Materials
- Tech Scout
- Unparalleled Data Quality
- Higher Quality Content
- 60% Fewer Hallucinations
Browse by: Latest US Patents, China's latest patents, Technical Efficacy Thesaurus, Application Domain, Technology Topic, Popular Technical Reports.
© 2025 PatSnap. All rights reserved.Legal|Privacy policy|Modern Slavery Act Transparency Statement|Sitemap|About US| Contact US: help@patsnap.com