Aluminum rolling composite additive and preparation method thereof
A composite additive and aluminum rolling technology, applied in lubricating compositions, petroleum industry, etc., can solve problems such as low surface quality of annealed products, prolong annealing time, increase annealing energy consumption, etc., to improve product surface quality and reduce friction coefficient , the effect of increasing the annealing temperature
- Summary
- Abstract
- Description
- Claims
- Application Information
AI Technical Summary
Problems solved by technology
Method used
Image
Examples
preparation example Construction
[0044] refer to figure 1 , the present invention also provides a kind of preparation method of aluminum rolling compound additive, comprises the steps:
[0045] Step 1 S100, formulating the components of the aluminum rolling composite additive according to the mass percentage;
[0046] Step 2 S200, mixing the decanyl alcohol, lauryl alcohol and myristyl alcohol formulated according to the mass percentage and preparing the mixed alcohol additive with the mass percentage;
[0047] Step 3 S300, mixing the methyl myristate and methyl palmitate formulated according to the mass percentage and preparing the mixed fatty acid ester additive in the mass percentage;
[0048] Step 4 S400, sequentially add the mixed alcohol additive, mixed fatty acid ester additive and aluminum rolling base oil in the mass percentage into the blending kettle, and stir at 50° C. for 4 hours until the mixture is completely dissolved;
[0049] Step 5 S500, obtaining the composite additive for aluminum rolli...
Embodiment 1
[0054] A composite additive for aluminum rolling, comprising the following components: 13.0kg dedecyl alcohol, 20.0kg lauryl alcohol, 32.0kg myristyl alcohol, 20.0kg methyl myristate, 5.0kg methyl palmitate, 10.0kg aluminum rolling base oil kg.
[0055] The preparation method steps of above-mentioned composite additive for aluminum rolling are as follows:
[0056] Preparing the components of the aluminum rolling composite additive according to the quality;
[0057] 13.0kg of decanyl alcohol, 20.0kg of dodecanol and 32.0kg of myristyl alcohol were mixed and prepared into 65.0kg of mixed alcohol additive;
[0058] The methyl myristate of 20.0kg, the methyl palmitate of 5.0kg are mixed and prepared into the mixed fatty acid ester additive of 25.0kg;
[0059] Add 65.0kg of mixed alcohol additives, 25.0kg of mixed fatty acid ester additives and 10.0kg of aluminum rolling base oil into the blending kettle in turn, and stir at 50°C for 4 hours until the mixture is completely dissol...
Embodiment 2
[0062] A composite additive for aluminum rolling, comprising the following components: decanyl alcohol 15.0kg, lauryl alcohol 23.0kg, myristyl alcohol 37.0kg, methyl myristate 10.5kg, methyl palmitate 4.5kg, aluminum rolling base oil 10.0 kg.
[0063] The preparation method steps of above-mentioned composite additive for aluminum rolling are as follows:
[0064] Preparing the components of the aluminum rolling composite additive according to the quality;
[0065] 15.0kg of decanyl alcohol, 23.0kg of dodecanol and 37.0kg of myristyl alcohol were mixed and prepared into 75.0kg of mixed alcohol additive;
[0066] The methyl myristate of 10.5kg, the methyl palmitate of 4.5kg are mixed and prepared into the mixed fatty acid ester additive of 15.0kg;
[0067] Add 75.0kg of mixed alcohol additives, 15.0kg of mixed fatty acid ester additives and 10.0kg of aluminum rolling base oil into the blending kettle in turn, and stir at 50°C for 4 hours until the mixture is completely dissolve...
PUM
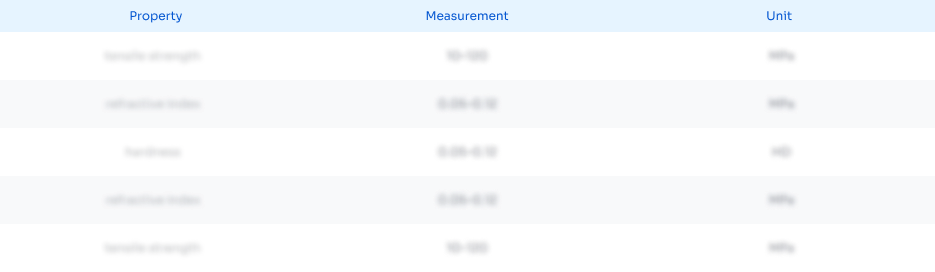
Abstract
Description
Claims
Application Information

- R&D
- Intellectual Property
- Life Sciences
- Materials
- Tech Scout
- Unparalleled Data Quality
- Higher Quality Content
- 60% Fewer Hallucinations
Browse by: Latest US Patents, China's latest patents, Technical Efficacy Thesaurus, Application Domain, Technology Topic, Popular Technical Reports.
© 2025 PatSnap. All rights reserved.Legal|Privacy policy|Modern Slavery Act Transparency Statement|Sitemap|About US| Contact US: help@patsnap.com