Technological method for sizing dyed weft yarns
A process method and technology of weft yarns, which are applied in the field of sizing of yarn-dyed weft yarns, can solve the problems of easy breakage, poor cloth surface effect, and low weaving efficiency, and achieve the effects of increasing strength, improving weaving efficiency and cloth surface effect, and reducing hairiness
- Summary
- Abstract
- Description
- Claims
- Application Information
AI Technical Summary
Problems solved by technology
Method used
Image
Examples
Embodiment 1
[0007] Embodiment 1: select 200kg pure cotton weft yarn for use, and the yarn count is 10 English count single yarns. Its technical solution is:
[0008] Step 1) For normal bobbin dyeing, the softening process is to add smoothing agent and cycle dyeing for 5 minutes;
[0009] Step 2) The liquid slurry adopts the acrylate liquid slurry QB-918J produced by Qingdao Jimo Qingbao Slurry Factory, adds 10kg of liquid slurry with a solid content of 25%, and processes for 5 minutes;
[0010] Step 3) After normal drainage and dehydration, enter the drying process.
[0011] Comparison of indicators before and after sizing of weft yarn package
[0012]
Embodiment 2
[0013] Embodiment 2: select 300kg pure cotton weft yarn bobbins for use, and the yarn count is 40 English single yarns, and its technical scheme is:
[0014] Step 1) For normal bobbin dyeing, the softening process is to add smoothing agent and cycle dyeing for 8 minutes;
[0015] Step 2) The liquid slurry adopts PVA (PVA-217MB Japan) with a concentration of 100g / L, adds 3kg, and processes for 8 minutes;
[0016] Step 3) After normal drainage and dehydration, enter the drying process.
[0017] Comparison of indicators before and after sizing of weft yarn package
[0018]
Embodiment 3
[0019] Embodiment 3: Select 100kg of T / C weft yarn bobbins, and the yarn count is 45 British count single yarns. Its technical solution is:
[0020] Step 1) For normal bobbin dyeing, the softening process is to add smoothing agent and cycle dyeing for 10 minutes;
[0021] Step 2) The liquid slurry adopts the acrylate liquid slurry QB-918J produced by Qingdao Jimo Qingbao Slurry Factory, adds 2 kg of liquid slurry with a solid content of 25%, and processes for 10 minutes;
[0022] Step 3) After normal drainage and dehydration, enter the drying process.
[0023] Comparison of indicators before and after sizing of weft yarn package
[0024]
PUM
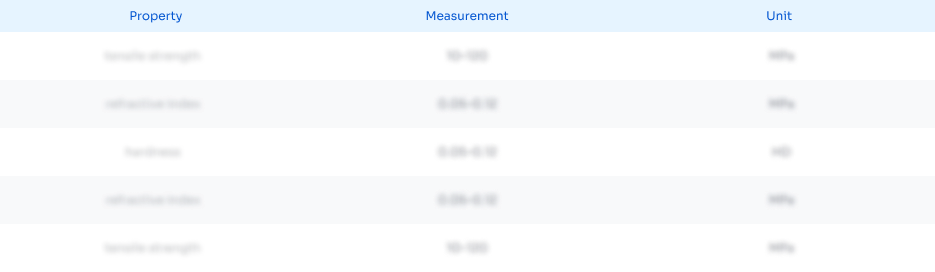
Abstract
Description
Claims
Application Information

- R&D Engineer
- R&D Manager
- IP Professional
- Industry Leading Data Capabilities
- Powerful AI technology
- Patent DNA Extraction
Browse by: Latest US Patents, China's latest patents, Technical Efficacy Thesaurus, Application Domain, Technology Topic, Popular Technical Reports.
© 2024 PatSnap. All rights reserved.Legal|Privacy policy|Modern Slavery Act Transparency Statement|Sitemap|About US| Contact US: help@patsnap.com