Improved blast furnace coal injection tank and injection method
A blast furnace coal injection and coal injection tank technology, which is applied to blast furnaces, blast furnace details, blast furnace parts, etc., can solve the problems of large pressure changes in the coal injection tank, fluctuations in injection rate, and long coal charging time, so as to improve the accuracy. and uniformity, reduce consumption and equipment damage, and improve the effect of injection stability
- Summary
- Abstract
- Description
- Claims
- Application Information
AI Technical Summary
Problems solved by technology
Method used
Image
Examples
Embodiment Construction
[0021] Figure 2-Figure 3 It shows that an improved blast furnace coal injection tank of the present invention comprises a pulverized coal bin 1 and a coal injection tank 2 communicated with each other through a communication pipe 3, and a lower coal valve 4 and a coal inlet valve 5 are respectively installed on the communication pipe 3. The lower part of the coal valve 4 is connected to a nitrogen purge pipe 31, on which a nitrogen purge valve 32 is installed; between the lower coal valve 4 and the coal inlet valve 5, there is a powder return pipe 6 directly connected to the pulverized coal bin 1, and a powder return pipe 6 is installed Gas filter screen 36; the top of the coal injection tank 2 is provided with a large diffuser 7, a medium diffuser 8 and a small diffuser 9, and the coal injection tank 2 is provided with a fluidization plate 10, a pressure-stabilizing fluidization hole 26, and an upper cone successively from top to bottom. Fluidization holes 11, lower cone flu...
PUM
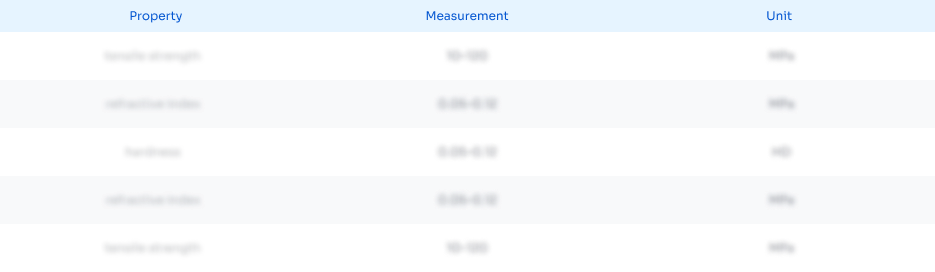
Abstract
Description
Claims
Application Information

- R&D Engineer
- R&D Manager
- IP Professional
- Industry Leading Data Capabilities
- Powerful AI technology
- Patent DNA Extraction
Browse by: Latest US Patents, China's latest patents, Technical Efficacy Thesaurus, Application Domain, Technology Topic, Popular Technical Reports.
© 2024 PatSnap. All rights reserved.Legal|Privacy policy|Modern Slavery Act Transparency Statement|Sitemap|About US| Contact US: help@patsnap.com