A kind of production process of porous or hollow porcelain wall tiles and porcelain blocks
A production process and hollow technology, applied in the production process of porcelain blocks, in the field of porous or hollow ceramic wall tiles, can solve the problems of affecting the decorative effect and service life, affecting the appearance of products, falling off the glaze layer, etc., to shorten the construction period, Reduces overall weight and does not fall off easily
- Summary
- Abstract
- Description
- Claims
- Application Information
AI Technical Summary
Problems solved by technology
Method used
Examples
Embodiment 1
[0020] First crush red shale and coal gangue to a particle size of ≤2.5mm, of which more than 70% of the particles have a particle size of ≤1mm, then add water and stir evenly according to the weight ratio of red shale:coal gangue of 4.5:1, and make The green body material, the ratio of raw material to water is 1:0.1; then the green body material is sent to the double-stage hard plastic vacuum extruder through the conveyor belt to be extruded into a billet, the extrusion pressure is 4.0Mpa, and the molding moisture content is 13%; send the billet into the brick cutter or block machine to cut into the adobe body; then put the adobe body on the rail car through the automatic grabbing machine, and the cut surface of the adobe body is on both sides; The green body is sent to the drying kiln for drying, the drying temperature is 80°C, and the humidity of the green body after drying is 9.5%; then the dried green body is turned over, and the contact surface between the green body and ...
Embodiment 2
[0022] First, crush red shale and coal gangue until the particle size is ≤2.5mm, of which more than 70% of the particle size is ≤1mm, then add water and stir evenly according to the weight ratio of red shale:coal gangue is 3.5:1, and make The green body material, the weight ratio of raw material and water is 1:0.1; then the green body material is sent to the vacuum extruder through the conveyor belt to be extruded into a billet, the extrusion pressure is 4.0 Mpa, and the molding moisture content is 16%. Send the billet into the brick cutter or block machine to cut the adobe body; then put the adobe body on the rail car through the automatic grabbing machine, and the cut surface of the adobe body is on both sides; then the rail car sends the adobe body on the car to Put it into a drying kiln for drying, the drying temperature is 150°C, and the humidity after drying is 10.5%; then turn the dried green body over, and adjust the contact surface between the green body and the green ...
PUM
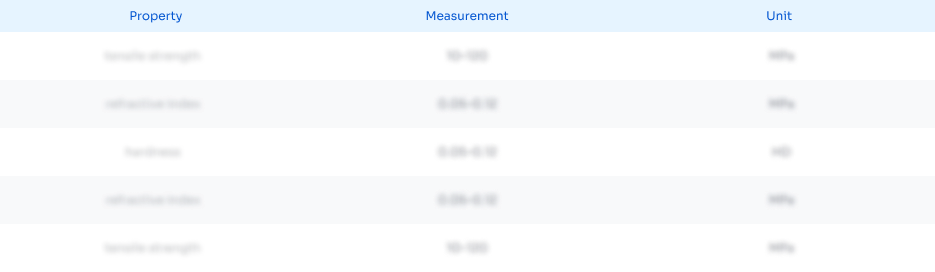
Abstract
Description
Claims
Application Information

- R&D Engineer
- R&D Manager
- IP Professional
- Industry Leading Data Capabilities
- Powerful AI technology
- Patent DNA Extraction
Browse by: Latest US Patents, China's latest patents, Technical Efficacy Thesaurus, Application Domain, Technology Topic, Popular Technical Reports.
© 2024 PatSnap. All rights reserved.Legal|Privacy policy|Modern Slavery Act Transparency Statement|Sitemap|About US| Contact US: help@patsnap.com