Butt joint method for long powder metallurgy compressed billets
A powder metallurgy, long-size technology, which is applied in the field of long-size powder metallurgy compact butt jointing, can solve problems such as the inability to suppress the density of the compact, and the size of the cemented carbide product is too long, and achieve the same mechanical properties and consistent density.
- Summary
- Abstract
- Description
- Claims
- Application Information
AI Technical Summary
Problems solved by technology
Method used
Examples
Embodiment Construction
[0012] A long-sized powder metallurgy compact butt joint method, comprising the following steps: first press the powder material with the grade YG15 and the wax ratio of 2.5% into two compacts with a diameter of 100mm and a height of 70mm through a mold, and the shrinkage coefficient is controlled at 1.3; Use a blade or other sharp tools to roughen the end faces of the two compacts, then evenly apply 100g of powder of the same brand on the end faces, then wrap several layers with PE film, and position the two compacts; put them in the cold In the isostatic press, pressurize to 120MPa, hold the pressure for 10 minutes, and complete the splicing of the compact.
[0013] After splicing, check whether there are cracks at the connection by turning, and then check the condition of the joint after wax removal to see if there is any crack. If there is none, put it into the furnace and heat it at 1430°C for 1.5 hours to make a finished product, and then inspect it to see if there are a...
PUM
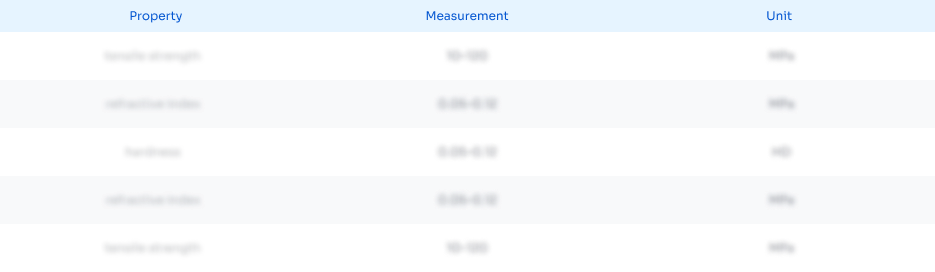
Abstract
Description
Claims
Application Information

- R&D
- Intellectual Property
- Life Sciences
- Materials
- Tech Scout
- Unparalleled Data Quality
- Higher Quality Content
- 60% Fewer Hallucinations
Browse by: Latest US Patents, China's latest patents, Technical Efficacy Thesaurus, Application Domain, Technology Topic, Popular Technical Reports.
© 2025 PatSnap. All rights reserved.Legal|Privacy policy|Modern Slavery Act Transparency Statement|Sitemap|About US| Contact US: help@patsnap.com