Centrifugal casting method for composite ring with Q345B steel inner layer and 40Cr steel outer layer
A Q345B, centrifugal casting technology, applied in the field of ring parts casting, can solve problems such as reducing service life and affecting processing, and achieve the effects of increasing service life, improving wear resistance, and uniform stress distribution
- Summary
- Abstract
- Description
- Claims
- Application Information
AI Technical Summary
Problems solved by technology
Method used
Examples
Embodiment Construction
[0011] Centrifugal casting is now performed on the composite ring with the material of the inner ring blank being Q345B and the material of the outer ring blank being 40Cr. The process steps are:
[0012] (1) The inner layer Q345B steel and the outer layer 40Cr steel of the composite ring are smelted in separate furnaces at the same time, and the furnace temperature of the Q345B steel is controlled to be 1650 ° C, and the temperature of the 40Cr steel is controlled to be 1600 ° C;
[0013] (2) Mold preheating: The mold preheating temperature is 150°C, and the mold is sprayed with silica sol, the spray thickness is 3.0mm, and asbestos pads with high temperature resistance ≥ 1600°C are installed on the end faces, ladles and runners The preheating temperature is 300°C;
[0014] (3) Pouring the outer layer: the pouring temperature is 1520°C, the mold speed is controlled at 230r / min, and the pouring speed is controlled at 24.5kg / s. After the outer layer is poured, the surface is co...
PUM
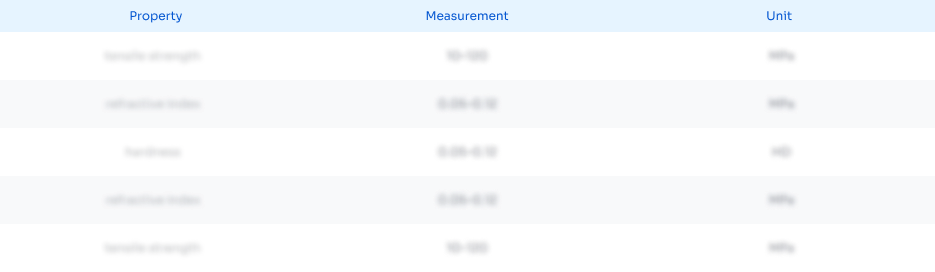
Abstract
Description
Claims
Application Information

- R&D
- Intellectual Property
- Life Sciences
- Materials
- Tech Scout
- Unparalleled Data Quality
- Higher Quality Content
- 60% Fewer Hallucinations
Browse by: Latest US Patents, China's latest patents, Technical Efficacy Thesaurus, Application Domain, Technology Topic, Popular Technical Reports.
© 2025 PatSnap. All rights reserved.Legal|Privacy policy|Modern Slavery Act Transparency Statement|Sitemap|About US| Contact US: help@patsnap.com