High-sheet resistance cell slice diffusion preparation method
A high square resistance, solar cell technology, applied in the direction of circuits, photovoltaic power generation, electrical components, etc., can solve the problems of low square resistance, low efficiency of solar cells, high doping concentration on the surface, etc.
- Summary
- Abstract
- Description
- Claims
- Application Information
AI Technical Summary
Problems solved by technology
Method used
Image
Examples
Embodiment 1
[0049] Embodiment one, adopt the diffusion method provided by the present invention:
[0050] Place the silicon wafer to be processed in a diffusion furnace, and at the same time, pass in oxygen at 700°C to 800°C, and the atmosphere in the furnace is a nitrogen atmosphere. The oxygen flow rate is 0.3L / min~1.5L / min. The time for passing gas into the diffusion furnace is 5 minutes to 7 minutes.
[0051] After the temperature stabilizes, continue to feed oxygen, wherein the oxygen flow rate is increased by 0.3L / min compared with the previous step; at the same time, feed phosphorus-carrying source gas and nitrogen gas for pre-deposition, and the nitrogen flow rate is reduced by 0.3L / min compared with the previous step . The ventilation time lasts 7 minutes to 10 minutes.
[0052] Raise the temperature to 800°C-900°C, continue to introduce phosphorus-carrying source gas and nitrogen, and continue to increase the oxygen flow rate by 0.3L / min on the basis of the previous step, while...
Embodiment 2
[0057] Embodiment two, adopt conventional diffusion process:
[0058] Place the silicon wafer to be processed in a diffusion furnace, and at the same time, under low temperature conditions, a sufficient amount of constant flow of oxygen is introduced, and the furnace is surrounded by a nitrogen atmosphere.
[0059] When the temperature is stable, continue to feed oxygen with a constant flow rate, and simultaneously feed phosphorus-carrying source gas and nitrogen for pre-deposition.
[0060] Stop feeding the phosphorus-carrying source gas and dry oxygen, continue feeding nitrogen, and raise the temperature for 5 minutes.
[0061] After the temperature rises, continue to introduce phosphorus-carrying source gas, dry oxygen and nitrogen to carry out step-by-step trap pushing. The trap pushing time is 30 minutes, and the flow rate of dry oxygen remains unchanged.
[0062] Cool down and leave the boat to complete the diffusion process.
[0063] The silicon chip that embodiment t...
PUM
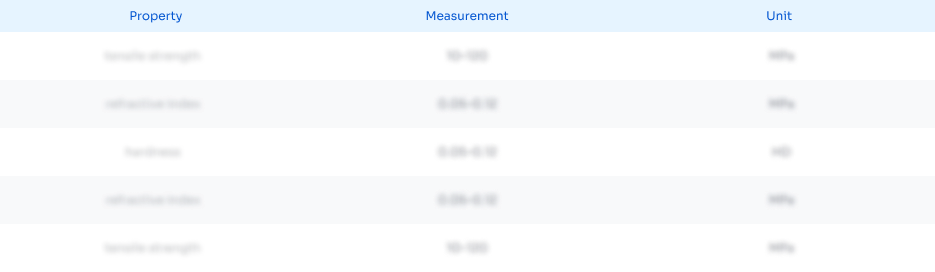
Abstract
Description
Claims
Application Information

- R&D
- Intellectual Property
- Life Sciences
- Materials
- Tech Scout
- Unparalleled Data Quality
- Higher Quality Content
- 60% Fewer Hallucinations
Browse by: Latest US Patents, China's latest patents, Technical Efficacy Thesaurus, Application Domain, Technology Topic, Popular Technical Reports.
© 2025 PatSnap. All rights reserved.Legal|Privacy policy|Modern Slavery Act Transparency Statement|Sitemap|About US| Contact US: help@patsnap.com