Pelletizing method for reducing bentonite consumption
A bentonite and pelletizing technology is applied in the field of pelletizing to reduce the consumption of bentonite, which can solve the problems of short expansion time, increased consumption of bentonite, and reduced pelletizing quality, and achieves improved pelletizing performance, reduced waste, and optimized particle size composition. Effect
- Summary
- Abstract
- Description
- Claims
- Application Information
AI Technical Summary
Problems solved by technology
Method used
Image
Examples
Embodiment 1
[0030] The pelletizing method for reducing the consumption of bentonite described in this embodiment uses bentonite as a binder, and includes the process steps of mixing, pelletizing, drying and preheating, and roasting. In the mixing step, the weight ratio is 50%. The mixture of Qinggangping concentrated ore powder and Xichangnan concentrate powder with a weight ratio of 50% is used as pelletized ore concentrate powder. When mixing materials, spray water on the surface of the bentonite, and the amount of water added is 1.5t / h, and then mixed with The spheroidizing concentrate powder is mixed, and the bentonite accounts for 1.4% of the total weight of the mixed powder.
[0031] The Qinggangping concentrate powder and the Xichangnan concentrate powder are dried before being mixed, and then crushed by a roller press. The particle size of the pulverized Qingbangping concentrate powder is: the weight ratio of passing through a 200-mesh sieve is 60-65%, the particle size of the pul...
Embodiment 2
[0034] The pelletizing method described in this embodiment to reduce the consumption of bentonite uses bentonite as a binder, including the process steps of mixing, pelletizing, drying, preheating, and roasting. The difference from the pelletizing method described in Embodiment 1 is:
[0035] In the mixing step, a mixture of 55% by weight of Qinggangping concentrate powder and 45% by weight of Xichangnan concentrate powder is used as the pelletizing concentrate powder. When mixing, the bentonite accounts for the 1.45% of the total weight of the mixed powder.
Embodiment 3
[0037] The pelletizing method described in this embodiment to reduce the consumption of bentonite uses bentonite as a binder, including the process steps of mixing, pelletizing, drying, preheating, and roasting. The difference from the pelletizing method described in Embodiment 1 is:
[0038] In the mixing step, a mixture of 60% by weight of Qinggangping concentrate powder and 40% by weight of Xichangnan concentrate powder is used as the ball concentrate powder. When mixing, the bentonite accounts for the 1.5% of the total weight of the mixed powder.
PUM
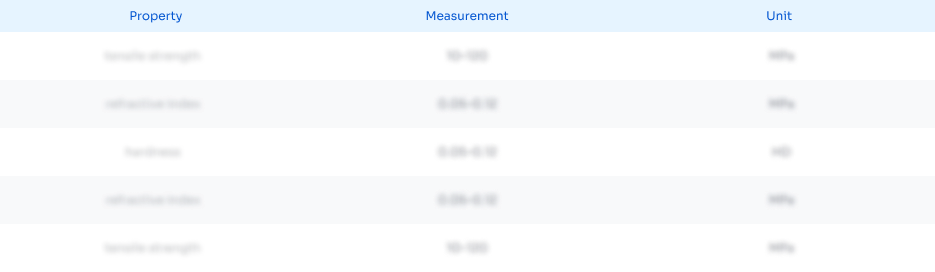
Abstract
Description
Claims
Application Information

- R&D
- Intellectual Property
- Life Sciences
- Materials
- Tech Scout
- Unparalleled Data Quality
- Higher Quality Content
- 60% Fewer Hallucinations
Browse by: Latest US Patents, China's latest patents, Technical Efficacy Thesaurus, Application Domain, Technology Topic, Popular Technical Reports.
© 2025 PatSnap. All rights reserved.Legal|Privacy policy|Modern Slavery Act Transparency Statement|Sitemap|About US| Contact US: help@patsnap.com