Laminated lithium battery aluminum shell structure and manufacturing method thereof
A manufacturing method and technology for lithium batteries, which are applied in structural parts, battery pack parts, battery boxes/jackets, etc., can solve problems such as high welding and assembly requirements
- Summary
- Abstract
- Description
- Claims
- Application Information
AI Technical Summary
Problems solved by technology
Method used
Image
Examples
Embodiment Construction
[0022] The present invention will be further described below in conjunction with the accompanying drawings.
[0023] An aluminum shell structure of a laminated lithium battery includes a shell wall 1 and a shell bottom 2, the shell bottom 2 is completely located in the shell wall 1, and a gap of 0-0.2 mm is left between one side and the shell wall 1; 2 and the shell wall 1 are welded by friction stir welding, and the friction stir welding seam runs along the joint between the shell bottom 2 and the shell wall 1 for a whole circumference.
[0024] A method for manufacturing an aluminum shell structure of a laminated lithium battery, which is characterized by comprising the following steps: S1. Sleeve the shell wall 1 outside the shell wall positioning column 4, and the lower part of the shell wall 1 is in contact with the positioning base 5; S2 , Put the shell bottom 2 in the space enclosed by the shell wall 1 and the upper surface 401 of the shell wall positioning column 4, an...
PUM
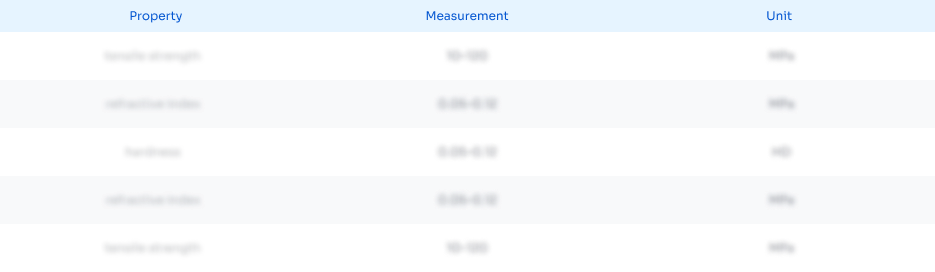
Abstract
Description
Claims
Application Information

- Generate Ideas
- Intellectual Property
- Life Sciences
- Materials
- Tech Scout
- Unparalleled Data Quality
- Higher Quality Content
- 60% Fewer Hallucinations
Browse by: Latest US Patents, China's latest patents, Technical Efficacy Thesaurus, Application Domain, Technology Topic, Popular Technical Reports.
© 2025 PatSnap. All rights reserved.Legal|Privacy policy|Modern Slavery Act Transparency Statement|Sitemap|About US| Contact US: help@patsnap.com