Polycrystalline silicon wafer texturing and cleaning method
A polycrystalline silicon wafer, mass concentration technology, applied in chemical instruments and methods, crystal growth, final product manufacturing, etc., can solve the problems of large optical loss, low conversion efficiency of solar cells, and large pits on the surface of polycrystalline silicon wafers
- Summary
- Abstract
- Description
- Claims
- Application Information
AI Technical Summary
Problems solved by technology
Method used
Examples
Embodiment 1
[0034] The polysilicon sheet texturing and cleaning method of embodiment 1 comprises the following steps:
[0035] (1) Soak the polysilicon wafer in the mixed solution at 2°C for 2 minutes for texturing. The mixed solution is composed of nitric acid, hydrofluoric acid and glacial acetic acid with a volume ratio of 15:5:2. The mass concentration of the nitric acid is 65% to 68%, and the purity of the nitric acid is industrial grade. The mass concentration of hydrofluoric acid is 48.4%-49.6%, and the purity of hydrofluoric acid is industrial grade. The mass concentration of glacial acetic acid is 99.8%-99.9%, and the purity grade of glacial acetic acid is electronic grade or analytical pure.
[0036] (2) The polysilicon wafer after texturing is sprayed and cleaned with ultrapure water, potassium hydroxide solution, mixed acid solution and ultrapure water in sequence. Wherein, the temperature of the potassium hydroxide solution is 48° C., and the mass concentration of potassiu...
Embodiment 2
[0039] The polysilicon sheet texturing and cleaning method of embodiment 2 comprises the following steps:
[0040] (1) Soak the polysilicon wafer in the mixed solution at 10°C for 1 minute for texturing. The mixed solution is composed of nitric acid, hydrofluoric acid and glacial acetic acid with a volume ratio of 14:4:1.5. The mass concentration of the nitric acid is 65% to 68%, and the purity of the nitric acid is industrial grade. The mass concentration of hydrofluoric acid is 48.4%-49.6%, and the purity of hydrofluoric acid is industrial grade. The mass concentration of glacial acetic acid is 99.8%-99.9%, and the purity grade of glacial acetic acid is electronic grade or analytical pure.
[0041] (2) The polysilicon wafer after texturing is sprayed and cleaned with ultrapure water, potassium hydroxide solution, mixed acid solution and ultrapure water in sequence. Wherein, the temperature of the potassium hydroxide solution is 52° C., and the mass concentration of potass...
Embodiment 3
[0044] The polysilicon chip texturing and cleaning method of embodiment 3 comprises the following steps:
[0045] (1) Soak the polysilicon wafer in the mixed solution at 5°C for 1.5 minutes for texturing. The mixed solution is composed of nitric acid, hydrofluoric acid and glacial acetic acid with a volume ratio of 15:5:2. The mass concentration of the nitric acid is 65% to 68%, and the purity of the nitric acid is industrial grade. The mass concentration of hydrofluoric acid is 48.4%-49.6%, and the purity of hydrofluoric acid is industrial grade. The mass concentration of glacial acetic acid is 99.8%-99.9%, and the purity grade of glacial acetic acid is electronic grade or analytical pure.
[0046] (2) The polycrystalline silicon wafers after texturing are sprayed and cleaned with ultrapure water, sodium hydroxide solution, mixed acid solution and ultrapure water in sequence. Wherein, the temperature of the sodium hydroxide solution is 50° C., and the mass concentration of...
PUM
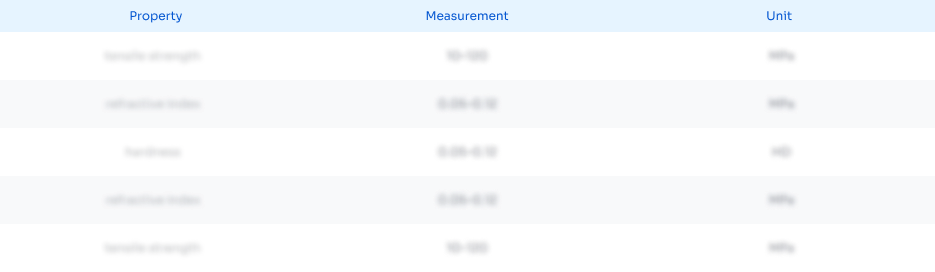
Abstract
Description
Claims
Application Information

- R&D
- Intellectual Property
- Life Sciences
- Materials
- Tech Scout
- Unparalleled Data Quality
- Higher Quality Content
- 60% Fewer Hallucinations
Browse by: Latest US Patents, China's latest patents, Technical Efficacy Thesaurus, Application Domain, Technology Topic, Popular Technical Reports.
© 2025 PatSnap. All rights reserved.Legal|Privacy policy|Modern Slavery Act Transparency Statement|Sitemap|About US| Contact US: help@patsnap.com