Metal composite plate rolling technique based on corrugated surface combining type blank forming
A metal composite plate and joint surface technology, which is applied in the field of billet rolling metal composite plate technology on the corrugated joint surface, can solve the problems of poor bonding performance of the composite interface, large residual stress, and cladding plate bending, etc., and achieve uniform deformation and residual The effect of small stress and large joint surface
- Summary
- Abstract
- Description
- Claims
- Application Information
AI Technical Summary
Problems solved by technology
Method used
Image
Examples
Embodiment 1
[0030] Attached figure 1 The method shown prepares carbon steel-copper composite panels.
[0031] Composite billet processing: Select Q345B carbon steel plate and TU2 copper plate to assemble billets according to the ratio of 3:1. The size of carbon steel plate is 120mm thick×3000mm wide×9000mm long as substrate 2, and the size of copper plate is 40mm thick×1500mm wide×3000mm long as doubler plate 1 , along the width direction, rolling arc-shaped corrugations that cooperate with each other on the composite surface of carbon steel plate and stainless steel composite surface respectively, the arc width is 200mm, the arc corrugation height is 20mm, and the arc corrugations are continuously distributed along the width direction; cleaning and rolling The corrugated surface of the carbon steel plate and the stainless steel plate is stacked, and the base plate 2 and the double plate 1 are stacked so that the corrugated surfaces of the carbon steel plate and the stainless steel plate...
Embodiment 2
[0034] Attached figure 2 The method shown prepares nickel steel-carbon steel-nickel steel double-sided composite panels.
[0035] Composite billet processing: Select N6 nickel steel plate, Q234R carbon steel plate and N6 nickel steel plate to assemble billets according to the ratio of 1:3:1. The size of carbon steel plate is 120mm thick×1500mm wide×3000mm long as the substrate 2’, and the size of nickel steel plate is 40mm thick× Two pieces of 3000mm in width and 9000mm in length are respectively used as the lower doubler board 3 and the upper doubler board 1', and the thickness of the sealing vertical board is 15mm. corrugated, the arc width is 300mm, the arc corrugation height is 20mm, and the arc corrugation is continuously distributed along the length direction; the corrugated surface of the rolled carbon steel plate and nickel steel plate is cleaned, and the lower cladding plate 3, the base plate plate 1', so that the corrugated surfaces of the carbon steel plate and th...
Embodiment 3
[0038] Attached image 3 The method shown is to prepare stainless steel-carbon steel clad plate.
[0039]Composite billet processing: Select Q235B carbon steel plate and 316L stainless steel plate to assemble billets according to the ratio of 4:1. The size of two Q235B carbon steel plates is 80mm thick×3000mm wide×9000mm long as substrates 5 and 7, and the size of two 316L stainless steel plates is 20mm thick ×Width 3000mm×Length 9000mm is used as doubler plates 4 and 6, and the thickness of the sealing vertical plate is 15mm. Along the length direction, the sinusoidal corrugations that cooperate with each other are rolled on the composite surface of Q235B carbon steel plate and 316L stainless steel plate respectively, and the height of the sinusoidal corrugation is 10mm. , the sinusoidal corrugation width is 200mm, and the sinusoidal corrugation is continuously distributed along the length direction; clean the corrugated surface of the rolled stainless steel plate and carbon ...
PUM
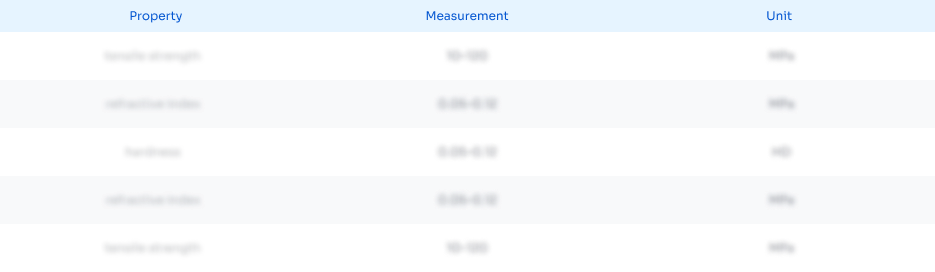
Abstract
Description
Claims
Application Information

- Generate Ideas
- Intellectual Property
- Life Sciences
- Materials
- Tech Scout
- Unparalleled Data Quality
- Higher Quality Content
- 60% Fewer Hallucinations
Browse by: Latest US Patents, China's latest patents, Technical Efficacy Thesaurus, Application Domain, Technology Topic, Popular Technical Reports.
© 2025 PatSnap. All rights reserved.Legal|Privacy policy|Modern Slavery Act Transparency Statement|Sitemap|About US| Contact US: help@patsnap.com