Hot continuous rolling intermediate billet thickness calculating method
A calculation method, hot continuous rolling technology, applied in the direction of metal rolling, metal rolling, length measuring device, etc., can solve the problems of decreased measurement accuracy, poor control accuracy, and low measurement accuracy, so as to achieve high safety and ensure measurement The effect of high accuracy and measurement accuracy
- Summary
- Abstract
- Description
- Claims
- Application Information
AI Technical Summary
Problems solved by technology
Method used
Image
Examples
Embodiment Construction
[0027] The specific implementation manners of the present invention will be described in detail below in conjunction with the accompanying drawings.
[0028] This implementation mode adopts a typical hot continuous rolling production line unit, and adopts the arrangement form of "rough rolling + finishing rolling" as follows: figure 1 As shown, the rough rolling is a reversible arrangement, and the finish rolling is a multi-stand continuous rolling arrangement; the time when the head and tail of the rolled piece pass through each instrument is as follows figure 1 As shown, between the roughing mill 7 and the finishing mill 8, a width gauge 5 behind the roughing mill, each hot metal detector (the first hot metal detector 1 and the second hot metal detector 2) behind the roughing mill are installed, and the finishing mill The hot metal detectors behind the finishing mill (the third hot metal detector 3 and the fourth hot metal detector 4), the thickness gauge 6 after the finishi...
PUM
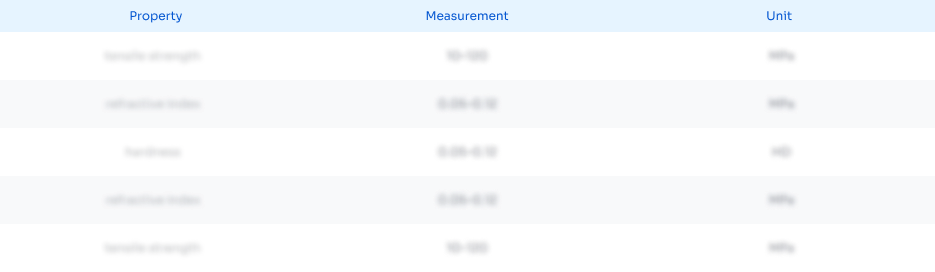
Abstract
Description
Claims
Application Information

- Generate Ideas
- Intellectual Property
- Life Sciences
- Materials
- Tech Scout
- Unparalleled Data Quality
- Higher Quality Content
- 60% Fewer Hallucinations
Browse by: Latest US Patents, China's latest patents, Technical Efficacy Thesaurus, Application Domain, Technology Topic, Popular Technical Reports.
© 2025 PatSnap. All rights reserved.Legal|Privacy policy|Modern Slavery Act Transparency Statement|Sitemap|About US| Contact US: help@patsnap.com