A kind of antimony composite flame retardant for silicate fiberboard and preparation method thereof
A composite flame retardant and fiberboard technology, which is applied in the fields of materials and chemicals, can solve the problems of limited use range and heavy weight, and achieve the effects of avoiding toxic and harmful gases and waste, improving production efficiency, improving fire resistance and processing performance
- Summary
- Abstract
- Description
- Claims
- Application Information
AI Technical Summary
Problems solved by technology
Method used
Image
Examples
Embodiment 1
[0024] Based on the total weight, weigh 50 parts of antimony trioxide, 30 parts of calcium silicate, 10 parts of zinc borate, 10 parts of hydrotalcite, and 5 parts of modifier.
[0025] The preparation method of antimony series composite flame retardant of the present invention comprises the following steps:
[0026] S1. Antimony trioxide modification: use titanate or aluminate to modify the surface of antimony trioxide, the modification temperature is 140°C, the stirring rate is 4000rpm / min, and the stirring time is 3.5h;
[0027] S2. Raw material mixing: put the modified antimony trioxide, calcium silicate, hydrotalcite, and zinc borate in the frequency conversion mixer for low-speed and high-speed two-stage uniform mixing. The stirring speed of low-speed mixing is 1200rpm / min, the mixing time is 5min, and the temperature is not controlled; the stirring speed of high-speed mixing is 5000rpm / min, the temperature is controlled at 100°C, and the mixing time is 20min;
[0028] ...
Embodiment 2
[0030] In total weight, 60 parts of antimony trioxide, 30 parts of calcium silicate, 4 parts of zinc borate, 3 parts of hydrotalcite, and 3 parts of modifier.
[0031] The preparation method of antimony series composite flame retardant of the present invention comprises the following steps:
[0032] S1. Antimony trioxide modification: use titanate or aluminate to modify the surface of antimony trioxide, the modification temperature is 100°C, the stirring rate is 2000rpm / min, and the stirring time is 4.5h;
[0033] S2. Raw material mixing: put the modified antimony trioxide, calcium silicate, hydrotalcite, and zinc borate in the frequency conversion mixer for low-speed and high-speed two-stage uniform mixing. The stirring speed of low-speed mixing is 600rpm / min, the mixing time is 10min, and the temperature is not controlled; the stirring speed of high-speed mixing is 2000rpm / min, the temperature is controlled at 70°C, and the mixing time is 40min;
[0034] S3. Screening: tran...
Embodiment 3
[0036] Based on the total weight, there are 60 parts of antimony trioxide, 20 parts of calcium silicate, 10 parts of zinc borate, 5 parts of hydrotalcite and 5 parts of modifier.
[0037] The preparation method of antimony series composite flame retardant of the present invention comprises the following steps:
[0038] S1. Antimony trioxide modification: use titanate or aluminate to modify the surface of antimony trioxide, the modification temperature is 120°C, the stirring rate is 3000rpm / min, and the stirring time is 4h;
[0039] S2. Raw material mixing: put the modified antimony trioxide, calcium silicate, hydrotalcite, and zinc borate in the frequency conversion mixer for low-speed and high-speed two-stage uniform mixing. The stirring speed of low-speed mixing is 900rpm / min, the mixing time is 8min, and the temperature is not controlled; the stirring speed of high-speed mixing is 3500rpm / min, the temperature is controlled at 85°C, and the mixing time is 30min;
[0040] S3...
PUM
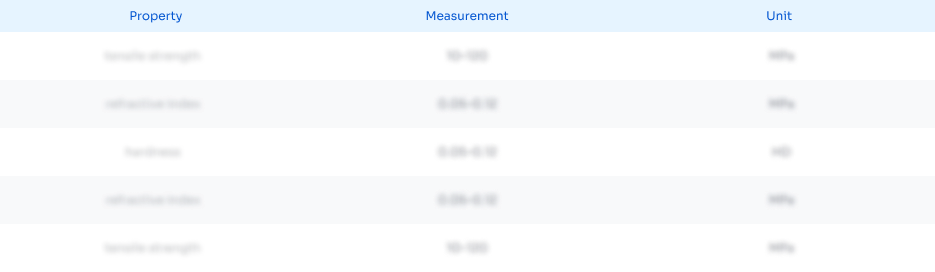
Abstract
Description
Claims
Application Information

- Generate Ideas
- Intellectual Property
- Life Sciences
- Materials
- Tech Scout
- Unparalleled Data Quality
- Higher Quality Content
- 60% Fewer Hallucinations
Browse by: Latest US Patents, China's latest patents, Technical Efficacy Thesaurus, Application Domain, Technology Topic, Popular Technical Reports.
© 2025 PatSnap. All rights reserved.Legal|Privacy policy|Modern Slavery Act Transparency Statement|Sitemap|About US| Contact US: help@patsnap.com