A two-dimensional vibration-assisted laser scanning in-position detection system and its detection method
An auxiliary laser and two-dimensional vibration technology, which is applied in the direction of measuring/indicating equipment, metal processing machinery parts, metal processing equipment, etc., can solve the problems of low detection efficiency, insufficient precision, high price, etc., achieve reliable detection accuracy and improve detection Accuracy, cost and error reduction effects
- Summary
- Abstract
- Description
- Claims
- Application Information
AI Technical Summary
Problems solved by technology
Method used
Image
Examples
Embodiment Construction
[0034] The present invention will be further described below in conjunction with the accompanying drawings.
[0035] Such as figure 1 Shown is an integration diagram of a specific implementation of the two-dimensional vibration-assisted laser scanning in-position detection system of the present invention and an ultra-precision grinding machine. Its detection object can be a large space mirror. The two-dimensional vibration-assisted laser scanning in-position detection system 20 is integrated on the main shaft of the grinding machine 21 and can move together with the main shaft. A grinder is a type of machine tool. The two-dimensional vibration-assisted laser scanning in-situ inspection system, such as figure 2 with 3As shown, it includes vibration platform base 1, motor fixed support 2, Y-axis voice coil motor 4, follow-up guide rail connector 13, follow-up guide rail 14, laser displacement sensor 6, Y-axis motion platform 15, Y-axis guide rail 8 , Y-axis grating 7, X-ax...
PUM
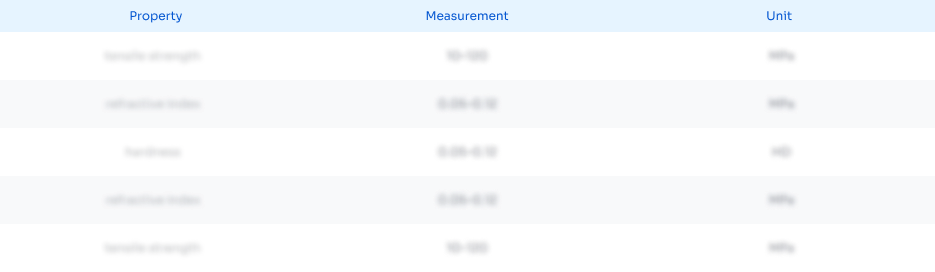
Abstract
Description
Claims
Application Information

- R&D
- Intellectual Property
- Life Sciences
- Materials
- Tech Scout
- Unparalleled Data Quality
- Higher Quality Content
- 60% Fewer Hallucinations
Browse by: Latest US Patents, China's latest patents, Technical Efficacy Thesaurus, Application Domain, Technology Topic, Popular Technical Reports.
© 2025 PatSnap. All rights reserved.Legal|Privacy policy|Modern Slavery Act Transparency Statement|Sitemap|About US| Contact US: help@patsnap.com