Preparation method for lithium cobalt oxide cathode slurry
A technology of positive electrode slurry and lithium cobalt oxide, which is applied in the direction of battery electrodes, electrical components, circuits, etc., can solve the problems of lithium battery performance impact, long-term treatment of conductive agents, equipment requirements and high wear, and achieve short preparation time , less equipment wear and lower production energy consumption
- Summary
- Abstract
- Description
- Claims
- Application Information
AI Technical Summary
Problems solved by technology
Method used
Image
Examples
Embodiment 1
[0026] With SP as the conductive agent and PVDF as the binder, according to LiCoO 2 :SP:PVDF=95.7:2.3:2.0 mass ratio, the solvent NMP is 65% of the total amount of the above components. The preparation steps are as follows:
[0027] 1. Put each component into the mixing tank to stir and disperse for 40 minutes, and scrape the powder on the mixing paddle and the barrel at the time of 20 minutes and 40 minutes;
[0028] 2. Add 55% of the total amount of NMP to the above stirred powder, stir and disperse for 70 minutes, and scrape the slurry on the stirring blade and the barrel at the time of 20 minutes, 40 minutes and 60 minutes, The slurry temperature is controlled between 25 and 35°C;
[0029] 3. Add 35% of the total amount of solvent to the above-mentioned high-viscosity stirred slurry, stir and disperse for 60 minutes, and scrape the slurry on the stirring blade and the barrel at the time of 23 minutes, 46 minutes and 70 minutes Material, the temperature of the slurry is ...
Embodiment 2
[0037] With SP and KS-6 as conductive agent, PVDF as binder, according to LiCoO 2 : SP: KS-6: PVDF = 93: 2.2: 1.3: 3.5 mass ratio, solvent NMP is 90% of the total amount of the above components. The preparation steps are as follows:
[0038] 1. Add each component into the mixing tank to stir and disperse for 30 minutes, and scrape the powder on the mixing paddle and the barrel at the time of 15 minutes and 30 minutes;
[0039] 2. Add 60% of the total amount of NMP to the above-mentioned stirred powder, stir and disperse for 60 minutes, and scrape the slurry on the stirring blade and the barrel at the time of 20 minutes, 40 minutes and 60 minutes, The slurry temperature is controlled between 25 and 35°C;
[0040] 3. Add 30% of the total amount of solvent to the above-mentioned high-viscosity stirred slurry, stir and disperse for 60 minutes, and scrape the slurry on the stirring blade and the barrel at the time of 20 minutes, 40 minutes and 60 minutes Material, the temperatur...
PUM
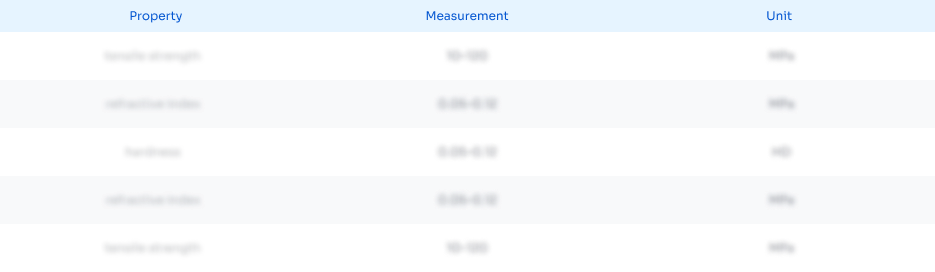
Abstract
Description
Claims
Application Information

- R&D Engineer
- R&D Manager
- IP Professional
- Industry Leading Data Capabilities
- Powerful AI technology
- Patent DNA Extraction
Browse by: Latest US Patents, China's latest patents, Technical Efficacy Thesaurus, Application Domain, Technology Topic, Popular Technical Reports.
© 2024 PatSnap. All rights reserved.Legal|Privacy policy|Modern Slavery Act Transparency Statement|Sitemap|About US| Contact US: help@patsnap.com