Chromium slag processing method
A treatment method, chromium slag technology, applied in the direction of improving process efficiency, etc., can solve the problems of complex process, secondary pollution, high treatment cost, etc., and achieve the effect of no secondary pollution, high strength, and effective resource saving
- Summary
- Abstract
- Description
- Claims
- Application Information
AI Technical Summary
Problems solved by technology
Method used
Examples
Embodiment 1
[0022] A method for treating chromium slag, comprising the steps of:
[0023] (1) Ingredients: weigh the chromium slag and raw coal, and blend them with a weight ratio of 1:9, then crush the mixture to make the fineness R 90 15%;
[0024] (2) Incineration and detoxification: spray the mixed material obtained in step (1) into the cyclone furnace with hot air for high-temperature incineration. The incineration temperature is 1600°C and the time is 2s; the temperature of the hot air is 160°C and the flow rate is 86888m 3 / h, the flow rate is 30-35m / s; the air volume ratio in the cyclone furnace is: primary air rate 16.9%, primary air temperature 237°C, primary air velocity 26.7m / s, primary air volume 86888m 3 / h; secondary air rate 62.3%, secondary air temperature 353°C, secondary air velocity 69.4m / s, secondary air volume 395277m 3 / h; the rate of the third wind is 20.8%, the temperature of the third wind is 60°C, the speed of the third wind is 55m / s, and the volume of the thi...
Embodiment 2
[0031] A method for treating chromium slag, comprising the steps of:
[0032] (1) Ingredients: weigh the chromium slag and raw coal, and blend them so that the chromium slag accounts for 4% of the total weight of the mixture, and then crush the mixture to make the fineness R 90 12%;
[0033] (2) Incineration and detoxification: spray the mixed material obtained in step (1) into a cyclone furnace with hot air for high-temperature incineration. The incineration temperature is 1400°C and the time is 5s; the temperature of the hot air is 150°C and the flow rate is 86888m 3 / h, the flow rate is 30-35m / s; the air volume ratio in the cyclone furnace is: primary air rate 16.9%, primary air temperature 237°C, primary air velocity 26.7m / s, primary air volume 86888m 3 / h; secondary air rate 62.3%, secondary air temperature 353°C, secondary air velocity 69.4m / s, secondary air volume 395277m 3 / h; the rate of the third wind is 20.8%, the temperature of the third wind is 60°C, the speed o...
Embodiment 3
[0040] A method for treating chromium slag, comprising the steps of:
[0041] (1) Ingredients: weigh the chromium slag and raw coal, and blend them so that the chromium slag accounts for 12% of the total weight of the mixture, and then crush the mixture to make the fineness R 90 20%;
[0042] (2) Incineration and detoxification: spray the mixed material obtained in step (1) into a cyclone furnace with hot air for high-temperature incineration. The incineration temperature is 1500°C and the time is 4s; the temperature of the hot air is 170°C and the flow rate is 86888m 3 / h, the flow rate is 30-35m / s; the air volume ratio in the cyclone furnace is: primary air rate 16.9%, primary air temperature 237°C, primary air velocity 26.7m / s, primary air volume 86888m 3 / h; secondary air rate 62.3%, secondary air temperature 353°C, secondary air velocity 69.4m / s, secondary air volume 395277m 3 / h; the rate of the third wind is 20.8%, the temperature of the third wind is 60°C, the speed ...
PUM
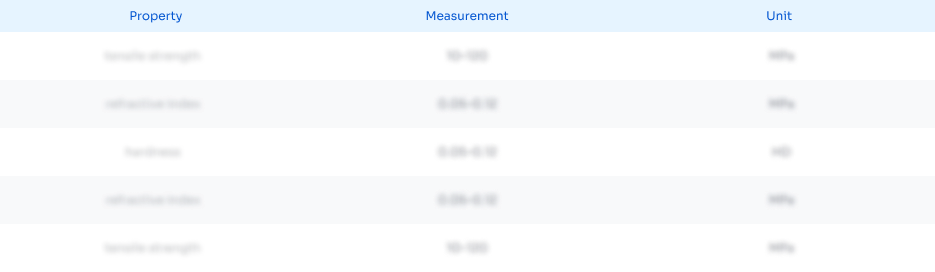
Abstract
Description
Claims
Application Information

- R&D Engineer
- R&D Manager
- IP Professional
- Industry Leading Data Capabilities
- Powerful AI technology
- Patent DNA Extraction
Browse by: Latest US Patents, China's latest patents, Technical Efficacy Thesaurus, Application Domain, Technology Topic, Popular Technical Reports.
© 2024 PatSnap. All rights reserved.Legal|Privacy policy|Modern Slavery Act Transparency Statement|Sitemap|About US| Contact US: help@patsnap.com