Pressing die and pressing process for welding neck flange
A high-neck flange, pressing die technology, applied in the direction of manufacturing tools, forging/pressing/hammering machinery, metal processing equipment, etc., can solve the problems of large machining allowance, easy inclusion, use, etc., and achieve excellent mechanical properties , Small machining allowance, the effect of uniform structure
- Summary
- Abstract
- Description
- Claims
- Application Information
AI Technical Summary
Problems solved by technology
Method used
Image
Examples
Embodiment Construction
[0025] The present invention will be further described through specific embodiments below in conjunction with the accompanying drawings.
[0026] As shown in the figure, a pressing die for a high neck flange includes an upper forming die 1 and a lower forming die 2 that are fastened up and down, and an expanding ball 3 for diameter expansion, and the upper forming die 1 and the lower forming die 2 are fastened together. After closing, it forms a cavity for high-necked flange molding. The upper molding die 1 is a circular cover plate provided with a core rod 101. The lower surface of the circular cover plate is provided with a circular pressing plate 102. The core rod 101 is vertical Set on the pressing plate 102, the central axis of the core rod 101, the center of circle of the circular cover plate and the center of circle of the pressing plate 102 are all on the same straight line, and an inner concave surface 103 is set at the end of the core rod 101, and the inner concave su...
PUM
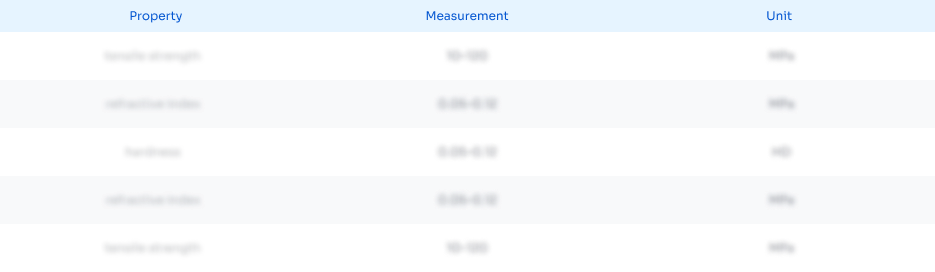
Abstract
Description
Claims
Application Information

- R&D Engineer
- R&D Manager
- IP Professional
- Industry Leading Data Capabilities
- Powerful AI technology
- Patent DNA Extraction
Browse by: Latest US Patents, China's latest patents, Technical Efficacy Thesaurus, Application Domain, Technology Topic, Popular Technical Reports.
© 2024 PatSnap. All rights reserved.Legal|Privacy policy|Modern Slavery Act Transparency Statement|Sitemap|About US| Contact US: help@patsnap.com